Research report 403 the influence of surface treatments on the service lives of concrete bridges
The influence of surface treatments
on the service lives of concrete bridges
SA Freitag
SM Bruce
Opus International Consultants Ltd, Lower Hutt
NZ Transport Agency research report 403
ISBN 978-0-478-36421-7 (print) ISBN 978-0-478-36420-0 (electronic) ISSN 1173-3756 (print) ISSN 1173-3764 (electronic)
NZ Transport Agency Private Bag 6995, Wellington 6141, New Zealand Telephone 64 4 894 5400; facsimile 64 4 894 6100
[email protected] www.nzta.govt.nz
Freitag, SA and SM Bruce (2010) The influence of surface treatments on the service lives of concrete bridges.
NZ Transport Agency research report 403. 91pp.
This publication is copyright NZ Transport Agency 2009. Material in it may be reproduced for personal or in-house use without formal permission or charge, provided suitable acknowledgement is made to this publication and the NZ Transport Agency as the source. Requests and enquiries about the reproduction of material in this publication for any other purpose should be made to the Research Programme Manager, Programmes, Funding and Assessment, National Office, NZ Transport Agency, Private Bag 6995, Wellington 6141.
Keywords: bridge asset management, chloride-induced corrosion, concrete, concrete bridges,
corrosion, preventive maintenance, reinforcement corrosion, silane, siloxane, surface treatments
An important note for the reader
The NZ Transport Agency is a Crown entity established under the Land Transport Management Act 2003. The objective of the Agency is to undertake its functions in a way that contributes to an affordable, integrated, safe, responsive and sustainable land transport system. Each year, the NZ Transport Agency funds innovative and relevant research that contributes to this objective.
The views expressed in research reports are the outcomes of the independent research, and should not be regarded as being the opinion or responsibility of the NZ Transport Agency. The material contained in the reports should not be construed in any way as policy adopted by the NZ Transport Agency or indeed any agency of the NZ Government. The reports may, however, be used by NZ Government agencies as a reference in the development of policy.
While research reports are believed to be correct at the time of their preparation, the NZ Transport Agency and agents involved in their preparation and publication do not accept any liability for use of the research. People using the research, whether directly or indirectly, should apply and rely on their own skill and judgement. They should not rely on the contents of the research reports in isolation from other sources of advice and information. If necessary, they should seek appropriate legal or other expert advice.
The authors acknowledge the contributions of representatives from the following organisations:
• Australian Paint Approval Scheme
• Alberta Transportation
• New South Wales Roads and Traffic Authority
• DIER Tasmania
• Queensland Main Roads
• Main Roads Western Australia
• Highways Agency (England)
• New Brunswick Department of Transportation
We also wish to thank past and present staff of Opus International Consultants (UK) Ltd for their insights into UK practice, particularly Mr S Hannaby, and the Australian consultant for his insights into Australian practice.
Contents
Executive summary.7
Abstract
Background .
Scope of the research .
Project details .
Surface treatments.
Types of surface treatment .
Types of penetrating sealer .
Hydrophobic pore liners .
Use of surface treatments by bridge-controlling authorities overseas .
3.1 Australia.
3.1.1 General .3.1.2 AS
Australian Paint Approval Scheme (APAS)
Tasmania Department of Infrastructure, Energy and Resources (DIER)
New South Wales Roads and Traffic Authority (RTA).
3.1.6 VicRoads .3.1.7
Queensland Main Roads (QMR) .
BS EN 1504-2 .
3.2.3 Experience
maintaining agents.
Wales and Scotland.
3.3 Canada/USA .
New Brunswick Department of Transportation (NBDoT)
Alberta Infrastructure and Transportation (Alberta Transportation) .
South Carolina Department of Transportation (SCDOT) .
Overall impressions from overseas experience.
Barriers to the use of silane/siloxane surface treatments .
Performance of surface treatments.
Evaluating surface treatments for use on New Zealand bridges .
Effect on water absorption/vapour permeability.
4.4 Carbonation .
Effect on chloride ingress .
Effect on corrosion activity.
Extension of service life .
Predicting service life.
Effects of surface treatments on other processes .
4.10 Overall benefits of surface treatments.
When and how to apply surface treatments .
The optimum time for intervention .
Identifying bridge populations that would benefit from surface treatments .
Identifying individual bridges that may benefit from surface treatments.
Specifying surface treatments for New Zealand bridges.
Maintenance after surface treatment .
Summary and conclusions.
Experience of road-controlling authorities overseas.
characteristics .
6.3.1 Silane/siloxane
6.3.2 Pore-blocking
Use for mitigating corrosion on New Zealand bridges.
Recommendations for NZ Transport Agency policy changes .
7.2 Recommendations
asset owners/managers.
References .
Appendices .
Appendix A Examples of specification limits.
Appendix B Deterioration of reinforced concrete.
Examples of deterioration models and limit states .
Appendix C Impact of cyclical maintenance on life cycle performance .
Executive summary
Background and scope of research
In New Zealand, more than 30% of state highway concrete bridges and more than 15% of local authority concrete bridges are over 50 years old. Although concrete bridge assets are generally performing well, it is recognised that reinforcement corrosion is a key deterioration mechanism, and that this deterioration is significantly more common in ageing coastal bridges. The costs of repairing these bridges to maintain their structural performance can be expected to increase in the future as the bridge stock ages.
The application of water-resistant surface treatments has been suggested as a means of delaying corrosion damage. In this research, carried out between 2007 and 2010, international research findings and the use of preventive surface treatments by road-controlling authorities in Australia, the UK and North America were reviewed to:
• develop a guideline for selecting appropriate surface treatments for delaying chloride-induced
corrosion damage on concrete road bridges in New Zealand
• develop a methodology for financially justifying the application of surface treatments, by
determining the influence of the treatments on the remaining service lives of bridges.
The research focused on the use of surface treatments that penetrate the concrete surface and reduce the ingress of moisture by lining or blocking pores, while allowing allow the concrete to dry. Penetrating surface treatments with potential for reducing corrosion induced by chloride ions include hydrophobic pore-lining treatments based on silanes and/or siloxanes, and pore-blocking treatments based on cementitious materials or alkali silicates.
International experience
Many road-controlling agencies permit existing concrete bridges to be treated with silane/siloxanes if the structures are at risk from chloride-induced corrosion from exposure to splash, spray, ponding or run-off from seawater or water containing de-icing salt. Some allow or require their use on new structures, but most prefer to address durability issues by managing the quality of concrete materials and construction.
The effectiveness of silane/siloxane treatments in reducing the ingress of moisture and chlorides and reducing corrosion activity depends on the composition of the product, the pore structure of the concrete, the moisture content of the concrete at the time of application, and the rate of application. Therefore most road-controlling agencies that permit their use specify requirements for the composition and performance of the products as supplied, application methods, and performance of the treated surface.
Barriers to the widespread uptake of silane/siloxane treatments include:
• justifying the cost of a preventive treatment
• environmental and health/safety concerns (potentially addressed by the recent introduction of
products supplied as creams or emulsions)
The influence of surface treatments on the service lives of concrete bridges
• the practical difficulties associated with ensuring the substrate is sufficiently dry when the
treatment is applied
• difficulties associated with managing the quality and consistency of the products and of their
Pore-blocking penetrating treatments are less widely accepted than silane-siloxanes, possibly because of difficulties in demonstrating that their performance will be satisfactory and in specifying appropriate acceptance criteria.
A risk- or value-based approach is generally preferred for determining the need to treat a structure. Detailed analyses of life cycle benefits and costs may be disproportionately expensive and time consuming compared to the cost of the treatment.
Performance characteristics
Silane and siloxane treatments may significantly reduce the ingress of moisture and chloride ions, thereby extending the time to chloride-induced corrosion. They also enable the concrete to dry, reducing the corrosion rate.
Silane and siloxane treatments need to be reapplied at regular intervals of 10–20 years, depending on exposure conditions and the depth of penetration. If maintained correctly, they may extend the service life of a structure for much longer than this, depending on the quality of application, exposure conditions, the degree of chloride ion contamination at the time of treatment, and the depth and quality of cover concrete.
Pore-blocking treatments tend to be less effective than hydrophobic treatments in reducing chloride and moisture ingress and corrosion activity, although they may be more effective where the concrete is immersed or exposed to groundwater, and in reducing carbonation.
Use for mitigating corrosion on New Zealand bridges
Silane and siloxane treatments have the potential to extend the service life of reinforced and prestressed concrete bridges if applied before corrosion damage occurs. Because they need to be applied regularly throughout the life of the structure, they will be most cost effective when applied when corrosion is imminent but no damage has yet occurred.
Current standards for the design and construction of concrete structures should deliver a 100-year service life without surface treatments. Good site supervision is essential to ensure that the depth and quality of concrete cover comply with the project specification.
Silane/siloxane treatments should not be applied to newly built structures because they may not be able to penetrate the surface sufficiently, may result in the concrete drying prematurely and therefore not achieving its potential ultimate performance, and will need to be reapplied at frequent intervals, adding extra maintenance costs. The exception to this is when they are applied as part of remedial works, should the quality of concrete or construction not meet specified requirements.
Similarly, preventive surface treatments should not be needed within 20 years of construction unless to manage localised corrosion of non-structural steel.
Structures most likely to benefit from silane/siloxane treatment are those at risk from corrosion induced by contamination with chloride ions from seawater or seaspray, ie those in the NZS 3101
Executive summary
exposure classifications B2 (coastal frontage) and C (tidal/splash/spray). Bridges in exposure classifications A2 and B1 are unlikely to benefit, except where features related to design or construction have led to corrosion of non-structural steel, or where localised corrosion of structural steel suggests a more widespread problem.
Within the population of bridges in the B2 and C exposure classifications, groups of bridges at increased risk from corrosion because of particular design features (eg prestressed, or with low cover depths), or exposure to particular microclimates will benefit the most.
Within these categories, individual bridges that may benefit from surface treatments are then identified by considering:
• the condition of concrete and reinforcement and how they would benefit from surface treatment
• the remaining service life required
• costs of access and other logistics
• whether it will be practical to maintain the treatment
• the effects on other surface treatments or remedial treatments that may subsequently be required.
Inspections to ascertain the potential benefits of treatment for a particular bridge should be carried out by specialists at least once every 20 years, in conjunction with Detailed Inspections.
The final decision to treat an individual bridge should not be based on economic evaluation alone, because an accurate evaluation is likely to cost a significant fraction of the treatment itself. In addition, NZ Transport Agency's current discount factor of 8% for maintenance works is unlikely to support preventive surface treatments on a life cycle benefit:cost basis. Instead, the decision-making process should involve a combination of economic evaluation and engineering judgement based on site investigation and testing to assess the actual condition of the structure and the risks of corrosion with and without surface treatment. If the NZ Transport Agency wishes to promote the use of preventive maintenance such as surface treatments, it should consider reducing the discount factor used for maintenance works.
Specifications for applying surface treatments to New Zealand bridges should be prepared by specialist consultants or based on APAS or other standard Australian specifications.
Once a preventive surface treatment has been applied, ongoing monitoring of its water resistance and of corrosion activity is required to ensure that the treatment is maintained at appropriate intervals. This monitoring should be carried out in conjunction with six-yearly Detailed Inspections. If the treatment is applied as a trial, such monitoring will indicate when untreated surfaces may need treatment or repair.
It is recommended that corrosion risk be addressed in a similar way to current seismic and scour risk-screening projects, whereby groups of bridges most at risk are identified, and then the needs of individual bridges within those groups are assessed in more detail to identify an appropriate means of addressing them.
The influence of surface treatments on the service lives of concrete bridges
In addition, it was recommended that the following NZ Transport Agency policies be amended to facilitate the screening process and the application of treatments where they are likely to minimise corrosion risk:
•
Regional Asset Management Plans amended to include mandatory investigations of bridges in
the following groups identified by this research as being at high risk from reinforcement or prestressing corrosion:
Bridges with localised corrosion that indicates that corrosion is likely to become more
widespread in the future.
Bridges more than 20 years old that are exposed to seawater splash or seaspray, ie in
NZS 3101 exposure classifications B2 (coastal frontage) or C (tidal/splash/spray). Prestressed structures within 200m of open surf are a particularly high priority.
•
The Bridge Inspection Policy amended to include Special Inspections for identifying the corrosion
risk on individual bridges.
•
Discount factors for maintenance works be reduced – this will demonstrate potential long-term
economic benefits more realistically and thereby facilitate the use of preventive treatments.
Recommendations were also made to guide asset managers and owners on how to evaluate the potential benefits of surface treatment for a particular structure or group of structures. Evaluations based on site investigations, experience, engineering judgement and simple predictions of service life, with and without treatment, are recommended for most cases, involving consideration of:
• concrete and reinforcement condition
• environmental exposure conditions
• extent of chloride ion contamination
• remaining service life requirements
• the practicalities of maintaining a treatment after application
• risk and costs associated with future reduced levels of service resulting from corrosion where
surface treatments are not applied or are not maintained
• the effect of surface treatments on other processes.
Brief guidance was also given on specification, acceptance and maintenance of surface treatments.
Abstract
The corrosion of reinforcing bars and prestressing steel is the most significant risk to the durability of concrete road bridges in New Zealand. The application of water-resistant surface treatments has been suggested as a means of delaying corrosion damage. This research, carried out between 2007 and 2010, reviewed international research findings and the use of preventive surface treatments by road-controlling authorities in Australia, the UK, and North America, to develop a guideline for selecting appropriate surface treatments for delaying chloride-induced corrosion damage on concrete road bridges in New Zealand.
The findings indicated that the effectiveness of surface treatments for reducing corrosion activity and extending service life depends not only on the chemical composition of the treatment, but also on the condition of the concrete substrate, the application process, and environmental exposure conditions.
A process was developed to identify the potential benefits of such surface treatments for individual bridges and for bridge populations.
Recommendations were made to help bridge owners and asset managers implement this process, including means of investigating concrete condition to complement economic evaluations, and considerations of monitoring and maintenance requirements for at-risk bridge elements before and after treatment.
In New Zealand, more than 30% of state highway concrete bridges and more than 15% of local authority concrete bridges are over 50 years old. Although concrete bridge assets are generally performing well, it is recognised that reinforcement corrosion is a key deterioration mechanism, and that this deterioration is significantly more common in ageing coastal bridges. The costs of repairing these bridges to maintain their structural performance can be expected to increase in the future as the bridge stock ages.
Recent Land Transport NZresearch, based on the assessment of 30 prestressed concrete bridge structures in the North Island (Bruce et al 2008), revealed that prestressing steel was starting to corrode in coastal bridges that were only 35–40 years old. Recent condition assessments by Opus for commercial clients have also detected corrosion of prestressing steel on several major bridge structures.
The corrosion of prestressing steel is more significant than the corrosion of conventional steel reinforcement because:
• structural failure may result, with little prior warning
• the repair of these structures is both difficult and expensive.
Because of this, Bruce et al (2008) recommended further investigation of proactive maintenance techniques, such as the use of surface treatments, to delay the onset of prestressing steel corrosion.
Asset owners and managers are currently in a difficult position. The accepted approach to the management of coastal bridges is to monitor the deterioration of the structures until the condition has reached a stage where repair is required. Many of the asset owners and managers are aware of some of the concrete surface treatments available, but the performance claims for these products are unsubstantiated and lack independence. Intuitively, this type of treatment offers significant potential for extending the service life of concrete bridges. However, the lack of guidelines for their selection makes it difficult for asset owners to make informed decisions about which treatments to use. The lack of a recognised methodology for establishing the influence of the treatment on the service life of a bridge makes it difficult to develop a robust financial argument for their use.
The need for such a methodology is becoming increasingly urgent. In addition to conventionally reinforced structures, the NZ Transport Agency and local authorities collectively own several hundred prestressed concrete bridges that were built in coastal environments in the 1960s and 1970s. Prestressing steel corrosion is likely to become increasingly common on these bridges as they age. The proactive maintenance of these bridges, using appropriate surface treatments, could delay the onset of prestressing steel corrosion (and the corrosion of conventional steel reinforcement as well), reducing the need for expensive concrete repairs and extending the life of these structures.
LTNZ, now the NZ Transport Agency.
The influence of surface treatments on the service lives of concrete bridges
The future transport environment will see the demands on bridge structures increasing. Bridges will be expected to last longer because of improved management and maintenance practices, and will also be expected to carry heavier vehicle loads. This research aimed to address both of these issues by developing improved practices for enhancing both the performance and service life of bridges, whilst reducing life cycle costs.
1.2 Scope of the research
The key objectives of the proposed research were:
1 to develop a guideline for the selection of appropriate concrete surface treatments for delaying the
onset of reinforcement corrosion in New Zealand road bridges
2 to develop a methodology for financially justifying the application of surface treatments, by
determining the influence of the treatments on the remaining service lives of bridges.
The research was based on a review of overseas developments in the performance and use of surface treatments for concrete. Recent international research findings about the performance of surface treatments were reviewed. Asset managers in key Australian road-controlling authorities were asked about their use of these treatments and how they decide when to apply them. The approaches taken by the UK trunk road agencies (including England's Highways Agency) and selected Canadian provinces were also reviewed because of their increasing use of coatings on bridge decks and supports to counteract the effects of de-icing salts on the durability of reinforced/prestressed concrete.
The research focused on the use of surface treatments to protect concrete surfaces exposed to seawater in the form of splash and spray – ie exposure classification B2 (coastal frontage) and part of exposure classification C as defined by NZS 3101:2006. Elements in these exposures were considered by Bruce et al (2008) to potentially benefit the most from surface treatments applied as a preventive measure.
A practical decision-making process was then developed to take into account the available data on the performance of surface treatments and the needs of asset managers to minimise both the life cycle costs of maintaining bridges and the risks associated with corrosion of reinforcing and prestressing steel.
Bruce et al (2008) assessed factors that contributed to corrosion risk on pre-tensioned elements. This current project considers the risk to reinforced and prestressed elements. Thus ‘prestressed' or ‘prestressing' herein refers to both pre-tensioning and post-tensioning, unless otherwise stated.
1.3 Project details
This research was carried out by Opus International Consultants Ltd between 2007 and 2010.
Surface treatments
2.1 Types of surface treatment
Surface treatments for concrete may be categorised in several ways:
• chemical composition – eg silane, siloxane, silicate, silicone, acrylic, epoxy, urethane, or
• function – eg aesthetic, barrier to liquid penetration, or barrier to gas penetration
• mechanism – eg hydrophobic pore lining, pore filling/blocking, or barrier coating
• physical form – eg penetrating sealer, barrier coatings that form a thin surface film, barrier
coatings that form a thick surface film or ‘membrane'.
Surface treatments for protecting against corrosion of steel reinforcement or prestressing need to reduce the ingress of moisture. Depending on whether carbonation or chlorides are the most likely cause of corrosion on a given structure, they also need to protect against the ingress of carbon dioxide and/or chloride ions.
This project focused on the risk of chloride-induced corrosion. Therefore it primarily considered surface treatments that reduce the ingress of moisture and chloride ions, rather than surface treatments that provide a barrier to carbon dioxide gas.
Surface treatments that form a barrier coating on the concrete surface rely on the barrier remaining intact and bonded to the concrete. Barrier coatings are susceptible to physical damage caused by impact, abrasion, and vapour pressure of water in the concrete. They must be able to withstand movement of the substrate caused by temperature changes or opening and closing of cracks. They are also exposed to chemical degradation/weathering by sunlight and water. Barrier coatings will also reduce the passage of gas into and out of the concrete. Thus they reduce the ingress of carbon dioxide (and thereby reduce carbonation), but they also prevent the concrete from drying, which may increase the risk of corrosion.
Surface treatments that penetrate the surface and line or block pores are less susceptible to physical damage and weathering than barrier coatings. Consequently, they may need less maintenance than a barrier coating to remain effective and to retain the appearance of the surface. Some allow the passage of gas, which reduces the corrosion risk by enabling the concrete to dry.
Such ‘penetrating sealers', sometimes called ‘impregnating sealers', are of interest to bridge asset managers in New Zealand and overseas because of their apparent durability and their ‘breathability'. Therefore this project only considered surface treatments that penetrate the concrete surface to line and/or block pores and voids. Surface treatments that form barrier coatings were not included.
Section 2.2 briefly describes penetrating sealers and how they work. Further information on these types of material, and on other surface treatments, is available in many other publications such as CIRIA (1987), The Concrete Society (1997), Song and Shayan (1999), and Bassi and Roy (2002).
The influence of surface treatments on the service lives of concrete bridges
2.2 Types of penetrating sealer
Penetrating sealers reduce the ingress of liquid water (which may contain dissolved salts, such as chloride ions) into the concrete from an exposed surface. They work by physically blocking fine pores in concrete or lining them with a hydrophobic layer. Their effectiveness depends on the size of the pores compared to the size of the sealer molecule (hydrophobic pore liners) or particle (pore blockers).
Song and Shayan (1999) consider that hydrophobic pore liners are effective for pores up to 0.02mm diameter, which includes gel pores and capillary pores in the cementitious binder. They consider that pore fillers are suitable for air voids up to about 0.1mm diameter, and that film-forming coatings should be used to deal with larger air voids, cavities and cracks.
2.2.1 Hydrophobic pore liners
Hydrophobic pore liners repel water but permit the flow of vapour, allowing the treated concrete to dry. The resulting reduction in internal moisture content of the concrete reduces the diffusion of ions (eg chlorides) into the concrete and increases electrical resistivity. Hydrophobic pore liners protect against the ingress of moisture from condensation, rain, run-off or ponding, but will not resist water that is applied under pressure. Therefore they are not suitable for immersed surfaces or those exposed to groundwater under pressure.
Most hydrophobic pore liners are silicon-based compounds. They include:
• silicone resins.
Siliconates are relatively cheap, water-based sealers designed for use with non-alkaline materials such as ceramics or gypsum-based products. They may also be used on masonry. They react with moisture and carbon dioxide to form a silicon polymer. If used on concrete, they may produce efflorescence as a by-product. The hydrophobic part of the molecule (see below) is not durable in alkaline conditions, so siliconates are not particularly effective for concrete.
Most hydrophobic pore liners for concrete are based on silane, siloxane, or a combination of both.
Silanes and siloxanes react with moisture, alkalis and silicates in the hydrated cement, producing silicon polymers. Although these polymers are akin to silicone resins, products based on silicone resins themselves are not as effective for improving the water resistance of good-quality concrete, because they do not penetrate fine pores and do not polymerise further after application.
In this report, ‘silane/siloxane' is a generic description of products based on either silane or
siloxane. The terms ‘silane', ‘siloxane' and ‘silane-siloxane' describe specific materials.
Silane molecules consist of single silicon atoms, attached to which are one or more organic alkyl groups (-CxHy or ‘-R') and up to three organic alkoxy groups (-O-CxHy or ‘-OR'). The alkyl groups are
stable and hydrophobic. The alkoxy groups react with moisture, alkali, other silane molecules, and
hydrated cement silicates to form a polymer that bonds to the cementitious binder. Alcohol is released as a by-product and evaporates without leaving a residue.
Siloxane molecules consist of short chains (‘oligomers') of alternating silicon and oxygen atoms. They are manufactured by condensing silane molecules together under controlled conditions. They have the same types of organic alkyl and alkoxy groups as silanes, and undergo the same bonding and polymerisation reactions, although their larger size and the consequently reduced penetration depth (see below) means that they tend to react with other siloxane molecules rather than with the hydrated cement.
Silanes and siloxanes are also known as alkyl alkoxy silanes/siloxanes, with the chemical names of the alkyl and alkoxy groups defining individual products. The particular combination of these groups defines the performance properties of individual products. Table 2.1 (on the next page) describes some of the widely used products.
The alkyl (‘R') group can range from methyl (the smallest) to octyl (the largest used in practice). The larger the alkyl group, the lower the volatility of the material and the better its pore-blocking ability and alkali resistance; the smaller the alkyl group, the better its penetration. Iso-butyl groups afford a good balance between penetration, alkali resistance and water repellency (Salome and Morris 1997). Some authorities have prohibited the use of methyl products, which have been identified as an eye hazard (Alberta Transportation 2009).
Methoxy (‘OR') groups are more reactive than ethoxy groups, and are more water-miscible. They release methanol when they react, however, whereas ethoxy groups release ethanol, which is less toxic.
Silanes, being smaller molecules, can penetrate smaller voids than siloxanes. Their small size also means they are more volatile, so when they are applied as a solution a significant portion can evaporate before it penetrates the concrete. Their monomeric nature means they are slower to polymerise. Consequently, when applied in windy and/or warm or low-humidity conditions, a significant amount of the silane may evaporate before it has reacted.
Siloxanes, being larger molecules, are more effective for filling larger voids. Ng (2006) suggests that siloxane chains longer than five silicon atoms are too large to penetrate effectively into the concrete and are therefore pore blockers rather than pore liners. Siloxanes are also less volatile and polymerise faster than silanes, so in windy and/or warm or dry conditions less material evaporates before it has reacted.
The influence of surface treatments on the service lives of concrete bridges
Table 2.1
Common types of silane (from data summarised by Song and Shayan 1999)
Chemical name
Specified by
Iso-octyl-tri-methoxy silane
• DoT Carolina (also
n-octyl-tri-methoxy
Iso-butyl-tri-methoxy silane
• Highways Agency
• DoT Carolina
Iso-butyl-tri-ethoxy silane
• Tasmania DIER
n-octyl-tri-ethoxy silane
(a) Australian Paint Approval Scheme specification (2009).
Many products are combinations of silane and siloxane. Such products are designed to optimise the greater penetration depth, water repellancy and durability generally offered by silanes together with the better pore-blocking ability and lower volatility generally offered by siloxanes.
The effectiveness of a particular product is determined by the pore structure of the substrate. Thus silanes/siloxanes with relatively small molecules are more appropriate for the fine pore structure of good-quality structural concrete; larger-moleculed siloxanes may be more appropriate for more porous concrete; and non-penetrating silicone sealers may be better for highly porous concrete such as masonry products.
Silanes and siloxanes are not miscible in water, so have historically been supplied dissolved in alcohol or hydrocarbon solvents. Siloxanes are typically supplied as dilute solutions (up to 20%). Silane solutions may be up to 100% silane or 100% silane liquid, or as creams or pastes in which they are emulsified with small amounts of water. These creams and 100% active products reduce the health and safety issues associated with using solvent-based products. In addition, the creams prevent rapid evaporation of the active ingredient (which can otherwise reduce the amount absorbed into the surface), allow application to soffit surfaces, and prevent problems associated with run-off or excess material pooling on horizontal surfaces.
Silane/siloxane treatments do not change the colour or texture of the treated surface, but they darken the surface, giving it a damp appearance. A sticky residue consisting of polymerised silicone resin may result if excess is applied.
2.2.2 Pore fillers/blockers/sealers
Apart from the larger-molecule siloxanes, penetrating sealers that fill or block the pores in the concrete are based on cementitious materials or alkali silicate solutions. Both types react with calcium hydroxide and water to form silicate-based products that reduce the movement of air, water vapour and liquid water through the concrete. Thus they may reduce the ingress of water and chloride ions and of carbon dioxide, thereby delaying the onset of corrosion induced by chloride ions or carbonation. They may reduce vapour transmission, but they are unlikely to reduce oxygen availability to a level where corrosion rates are reduced.
In this report, ‘silicate-based treatment' is a generic description of products that are based on
cementitious materials or silicate solutions.
Both types require water to react, so are applied to damp or wet substrates, and can be used on concrete in contact with groundwater, such as foundations or retaining walls. The cement-based products are used as waterproofers (ie to resist water under pressure) because of their pore-blocking ability and residual activity. They can be used to resist both positive and negative pressures, so can be used on either the upstream or downstream faces of water-retaining structures.
Silicate solutions may be used as a pre-treatment prior to the application of cement-based products (with the prior approval of the suppliers of both products).
The Portland cement-based products are often referred to as ‘crystalline' or ‘crystal forming'. They consist of finely ground Portland cement, silica fillers, and other constituents such as hydrated lime. When they come into contact with water, the cement reacts chemically in the same way as it does in concrete. The lime and silica filler will also react. When applied as a paste or slurry to the concrete surface, the soluble reaction products diffuse into the concrete pores, where they react with cement hydrates (calcium hydroxide and calcium alumino silicate hydrates) to form additional crystalline calcium alumino silicate hydrates. Some of these products may be added to fresh concrete as an admixture (this application is not covered by this project). Individual products are differentiated by the depth of penetration achieved and the structure of the crystalline hydrates produced.
The alkali silicates are solutions of sodium silicate, potassium silicate, or lithium silicate. They react with calcium hydroxide in the hydrated cement paste to form insoluble calcium silicate gels in the concrete pores. By reducing the amount of available calcium hydroxide, they further improve the concrete's acid and sulphate resistance. In addition to the initial chemical reaction, the silicate gels
The influence of surface treatments on the service lives of concrete bridges
(sometimes called ‘hydrogel') will also physically absorb water, preventing it from being transported through the concrete.
Silicate solutions may be less effective in concretes containing significant amounts of supplementary cementitious materials (SCMs) such as slag, fly ash and amorphous silica, because these materials reduce the amount of calcium hydroxide in the pore solution of the concrete. Similarly, they will be less effective in carbonated concrete. Although highly alkaline, they cannot be used to restore alkalinity to carbonated concrete.
In addition to their basic chemistry, both types of product may also contain other components, such as corrosion inhibitors, wetting agents and other additives to improve penetration of the product, or additives that modify the crystal or gel growth to improve its penetration and residual reactivity after application.
Once reacted, both types are integral with the hardened cement paste and cannot evaporate or be washed out.
Unreacted portions of the products will remain available in the concrete until they come into contact with sufficient moisture or alkalis, so they can remain effective for some time after application. Unreacted material remaining on the concrete surface can, however, be washed or worn away, like other barrier coatings.
Some silicate-based treatments are claimed to offer additional benefits or modes of action. Some examples are given below. We have suggested possible explanations for these claims, along with possible limitations. Our comments are intended to help specifiers evaluate the potential benefits of these products for their own applications, not to validate or dispute these claims.
• Some silicate solutions are claimed to ‘purge chlorides' from the concrete, which has led to their
promotion for mitigating chloride-induced corrosion. The claim probably arose because a crystalline material often appears on the concrete surface shortly after treatment. On one structure this was identified as sodium sulphate rather than sodium chloride (Peek and Ali 2001). It is thought to result from the sodium silicate reacting with calcium sulphate that originated from the cement.
• Another claim is that the chlorides are repositioned in the concrete, redistributing locally high
concentrations. This could happen as a result of silicate gel formation generating osmotic or hydrostatic pressures in the concrete pore system, or of chlorides being chemically bound within mobile gels. This repositioning may be beneficial in some cases, but there would be little control over where the chlorides are repositioned.
• Some products are claimed to neutralise or bind chlorides within the gel and thereby render them
unavailable to contribute to steel corrosion. Experiments conducted at an Australian site showed a reduction in both acid- and water-soluble chlorides three years after treatment (supplier's data), but a scientific mechanism for this has not been identified.
Such a binding mechanism may also bind other ions, thus reducing the conductivity of the pore solution. This would increase the electrical resistivity of the concrete and thereby reduce corrosion rates.
• One range of products claims that the penetrated material can promote crystal growth in cracks
that may form after its application, and that material remaining on the surface can be removed
without reducing the effectiveness of the treatment. The supplier promotes it as more suitable than similar products for concrete that is prone to movement. It should not, however, be applied to such structures without the supplier's approval.
Nevertheless, silicate-forming treatments should generally not be used to prevent the ingress of moisture, air or chemical contaminants into cracks because the treatment may not fully penetrate the cracks, particularly if the cracks are active. Similarly, these treatments should generally not be used on uncracked concrete that is expected to crack in the future, or on cracked concrete where the cracks are expected to become deeper, because the penetration depth may not be sufficient to protect concrete exposed by cracks that develop or deepen after treatment.
• Some suppliers have suggested that silicate-based treatments could be used to reduce expansion
of concrete affected by alkali silica reaction (ASR). If used for this purpose, the product must be based on lithium (rather than sodium or potassium, which may exacerbate ASR), and enough lithium must penetrate to sufficient depth within the concrete.
The influence of surface treatments on the service lives of concrete bridges
Use of surface treatments by bridge-
controlling authorities overseas
Selected agencies in Australia and Canada were contacted to find out about their use of surface treatment on concrete bridges. UK trunk road agencies' policies were also reviewed, along with recent recommendations from BRE.
This section presents information from these sources. The opinions expressed are those of the agencies/authors quoted, not the authors of this report.
The main cause of reinforcement corrosion in bridges in the US, Canada and the UK is chloride ion contamination from de-icing salts, whereas in New Zealand the main cause of reinforcement corrosion in bridges is exposure to chlorides of marine origin. Therefore, the risk to particular bridge elements is not the same in New Zealand as in most US, Canadian and UK bridges. Nevertheless, the practicalities of applying preventive surface treatments, and the barriers to their widespread use (ie cost, health, safety and environmental issues), are the same, irrespective of the origin of the chloride ions that increase the corrosion risk.
Representatives from state bridge authorities, as well as an independent consultant, indicated that treatments are usually applied once rebar corrosion has become evident, rather than as a preventive treatment. Treatments have been applied on bridges more than 40 years old, and as early as 10–15 years after construction on bridges exhibiting premature deterioration. They have also been used occasionally on new structures where problems such as inadequate cover or inappropriate concrete mix designs were detected during construction.
The independent consultant indicated that assessment of the need for a coating tends to be based on cost and on service life predictions from chloride ion profiles, considering factors such as:
• the age of the bridge
• the surface area of concrete in which rebar corrosion has already been initiated
• whether reducing moisture ingress from the treated surface will slow the corrosion rate
• whether reducing chloride ingress from the treated surface will slow the corrosion rate significantly
• accessibility for application and reapplication.
Most of the cost of applying a surface treatment is related to labour and access. The consultant estimated that the cost of materials could be as little as 10–15% of the contract price. Therefore he
2 The former Building Research Establishment.
Overseas use of surface treatments
considered that if the outer beams of a span need treatment, it may be worth treating the inner beams at the same time from a continuous scaffold, because they may eventually reach the same condition/level of contamination as the outer beams.
Concern about health/safety and environmental issues seemed to vary between states.
No experience of re-treating previously treated concrete was reported, reflecting that silanes and siloxanes have not been available much longer than 20 years, and that the expected lifetime of a treatment on a non-trafficked surface is at least 10 years (see section 4.7).
The durability provisions given in AS 4997-2005 for new maritime structures suggest that protective coatings be considered for protecting concrete members, but point out that the use of penetrating chloride ion inhibitors, such as silanes or siloxanes, precludes the use of chemical curing compounds.
AS 4997 suggests using additional protective measures, including hydrophobic surface sealants (silanes) or ‘other proven systems', to minimise chloride ion ingress where unprotected carbon steel wire or strand is used in pretensioned elements. Its general provisions for reinforcement cover depth suggest that in some circumstances, such surface treatments may be used in conjunction with cathodic protection. (It also suggests that non-prestressed carbon steel be located in the most exposed section of the element to provide an early indication of chloride-induced corrosion, and that this non-prestressed reinforcement should provide at least 40% of the total prestressed and non-prestressed reinforcement capacity.)
3.1.3 Australian Paint Approval Scheme (APAS)
Australian Paint Approval Scheme (APAS) specification AP-S0168 (2009) covers silane and siloxane water repellents for concrete and masonry. It defines four classes, as shown in table 3.1 (on the following page). Comments in sections 3.1.4–3.1.8 refer to the 2005 version of AP-S0168, but the 2009 specification is not significantly different.
APAS notes that the cost effectiveness of products within each class is not necessarily equivalent and suggests that, for direct comparison, the equivalent siloxane content of each should be taken into account (the specification describes how this is measured).
In addition to various properties of the products ‘as supplied', the specification includes requirements for their performance on concrete, including the:
• reduction in water uptake
• reduction in chloride ion penetration
• alkali resistance
• penetration depth.
It took several years to finalise the 2009 revision of AP S0168 because of difficulties in finding a universally applicable way to measure these properties.
The requirements were originally specified on the basis of performance on a 50MPa concrete made from prescribed materials and mix design. The 2009 revision is more practical, prescribing the water
The influence of surface treatments on the service lives of concrete bridges
to cement ratio, compressive strength and density. Specification of properties such as air content, porosity, sorptivity or absorption, as well as the above properties, may provide better control of the inherent quality of the concrete substrate.
Although the performance criteria are based on the performance of the materials on the prescribed concrete, it may be more practical to measure these properties on the concrete of interest: either concrete cored from an existing structure or, for a new structure, on specific concrete mix designs to be used. The disadvantage of this approach is that acceptance criteria would need to be established for the specific concrete.
Table 3.1
APAS classifications for silane/siloxane treatments
Subclass
TS0168/1
TS0168/2
TS0168/3
TS0168/4
Solvent-free silane
Silane solution in
Siloxane solution in
Silane cream at >75%
active silane in water
Iso-butyl or iso-octyl
Silane or silane-
Oligomeric siloxane
Octyl-tri-ethoxy silane
trialkoxy silane
siloxane mixture in
in organic solvent
in non-drip thixotropic
Alkoxy may be methoxy, ethoxy or propoxy
Undiluted (>95%)
of active constituent
Maximum protection
For general masonry
Maximum protection in
in marine or coastal
reinforced concrete/
in less critical
marine or coastal
concrete/masonry,
conditions, and non-
conditions, particularly
particularly to inhibit
alkaline substrates.
to inhibit rebar
rebar corrosion or
climates where high
Provides short-term
corrosion or mitigate
temperatures can't
protection and is
AAR. Suitable for most
less affected by
reinforced concrete
warm, dry and/or
structures in most
windy conditions
conditions (because
(performance criteria
of high volatility)
have not been specified)
(a) Alkali aggregate reaction.
(b) Including horizontal, vertical and overhead surfaces; warm, windy and dry weather.
3.1.4 Tasmania Department of Infrastructure, Energy and Resources (DIER)
An asset engineer from DIER reported that in the mid-1990s, DIER applied a combination of silane and anti-carbonation coatings as part of repairs on several bridges affected by corrosion on deck and beam soffits, to extend the life of the repairs. The bridges treated were mainly older than 50 years. Corrosion on coastal bridges was assumed to be related either to chlorides in the sand used to make the concrete, or to chlorides diffusing into the relatively poor-quality concrete. Corrosion on inland bridges was assumed to be related to carbonation. The extent of repair varied from patch repair of 5–10% of the soffit surface, to one complete soffit replacement; usually less than 30% of the surface needed repair. The effectiveness of the treatment was not assessed, but no further corrosion issues have been
Overseas use of surface treatments
reported in the 10 or so years since application. Repeat treatments have not been applied, although it was recognised that this would be needed.
DIER Specification B15 (2006) allows ‘protective coatings' to be applied to a repair ‘where required', and identifies three specific products as ‘acceptable' (all acrylic coatings). It requires protective coatings to be applied in accordance with Specification B23 (2006, also see below). The asset engineer expected coatings to approximately double the life of a patch repair. If the life of a patch repair is 10–15 years on concrete exposed to seaspray and 5–10 years on concrete in the splash zone (Freitag et al 2003), then observations suggest that the surface treatments have increased the service life of patch repairs in the most aggressive environments, and in less aggressive environments their effectiveness should become evident within the next few years. DIER does not apply surface treatments to bridges that are due for major rehabilitation or replacement within 5–10 years (ie one repair cycle), but apart from that, surface treatments are applied as part of the patch repair system.
The asset engineer thought that treatment may be more effective early in the life of a bridge, when the concentration of chlorides is lower and the effect of chlorides continuing to diffuse to the reinforcement after treatment would consequently be less. DIER had not yet applied surface treatments as a preventive measure.
DIER Specification B23 allows ‘methyl silane' or 100% isobutyl triethoxy silane, and silane-siloxane mixtures in organic carriers. It specifies physical properties for the silanes ‘as supplied', but not for the silane-siloxane mixtures. No performance requirements are specified, although provision is made for a pre-application trial on which penetration depth and absorption may be measured and the results used as a standard and control for the works. No requirements are specified for these properties, although the asset engineer said that the APAS specification was used. Both types of treatment may be overcoated with medium-build latex low-profile textured coating suitable for exterior concrete and masonry.
The method and rate of application is specified, including surface preparation and the use of a fugitive dye for monitoring application.
A proprietary ‘crystal growth' waterproofing product is also permitted, in a two-coat system.
3.1.5 New South Wales Roads and Traffic Authority (RTA)
The RTA has treated many structures with 100% isobutyl tri-ethoxy silane over the last 10 or so years to reduce the risk of chloride-induced corrosion. This material was chosen because it penetrated better than other materials.
Penetration depth is used as the key performance indicator, one of the assumptions being that the deeper the penetration, the more durable the treatment. Penetration is not expected to be as deep over repair materials as over the original concrete.
Observations of ongoing corrosion on parts of treated structures suggest that silanes are effective for concrete exposed to sea spray, but do not provide adequate protection in the splash zone. This was demonstrated by a sharp demarcation on a bridge pier, where reinforcement had corroded in the splash zone on previously treated concrete, but was in good condition above the splash zone.
Some bridges have been coated at construction time. One such bridge, exposed to sea spray, showed no signs of corrosion some 12 years later, and absorption tests showed that the surface treatment was
The influence of surface treatments on the service lives of concrete bridges
still effective. The rebar should indeed be in good condition after 12 years if construction was in accordance with an appropriate durability design, but the quality of the surface treatment after 12 years may have been better than anticipated.
A recent trial found that 100% silane liquids penetrated deeper at the specified application rates than creams, but that application rates were easier to control with creams. Multiple passes were needed to achieve the required application rates when spraying the silane liquids, each pass producing significant overspray. Creams are now preferred because they are easier to apply at the correct rate, with less waste and fewer associated health/safety and environmental problems.
Access costs may also sometimes be less with creams, which can be applied with a long-handled roller so the operator does not need to get as close as with a spray application.
One of the disadvantages of surface treatments is the surface preparation. Water cleaning at pressure is usually specified, but wash water has to be retained and safely discharged off site. Trials indicated that steam cleaning can give reasonable penetration depths, though not as good as pressure cleaning with water.
The RTA does not currently have a standard specification for surface treatments, instead relying on project-specific specifications. Key performance indicators are penetration depth, reduction in water uptake, and reduction in chloride ion uptake, determined from core samples by the methods specified in APAS 0168.
Recent surveys of the corrosion risk in the RTA's coastal bridges indicate that chloride-induced reinforcement corrosion is more likely on bridges built between 1959 and 1994 than on older or newer bridges (Chirgwin et al 2009). Of particular concern are bridges built between 1971 and 1994, when relatively high water to cement ratios were used and fly ash was not permitted in concrete. On these bridges, chloride ion contents in concrete in the tidal and splash zones were similar to those in the corresponding zones on bridges built between 1959 and 1970. Also, chloride ion contents in the atmospheric zone of several bridges built between 1971 and 1994 exceeded the threshold level for corrosion initiation, whereas chloride contents recorded in the atmospheric zone of bridges built between 1959 and 1970 were all less than the threshold level. As a result of these findings, the RTA now takes a fairly aggressive approach in order to reduce the risk of future corrosion. Thus for elements that are easily accessed, and where chloride contents have not yet reached threshold levels for corrosion initiation, it considers surface treatments without undertaking a detailed analysis. Where access costs are greater, a more detailed evaluation is carried out.
VicRoads has occasionally used silanes. The decision to treat a specific bridge has been subjective, based on consideration of costs, access and risk associated with the exposure conditions.
VicRoads Bridge Maintenance guidelines
VicRoads bridge maintenance repair and strengthening guidelines (VicRoads 2002) describe the main three uses of surface coatings as:
• to prevent deleterious substances permeating into the concrete (eg moisture, chlorides or carbon
Overseas use of surface treatments
• to seal the surface and regain the concrete cover protection lost by erosion of the surface skin of
Where surface treatments are applied to reduce chloride or moisture ingress, the Guidelines require the treatment to be permeable to water vapour so that the concrete can dry. Cementitious, moisture-cured polyurethane, silane, or silane-siloxane treatments are permitted, depending on the requirements of the treatment. It recommends polymer-modified cementitious fairing coats 3–5mm thick for sealing poor-quality surfaces and reducing chloride and moisture ingress, but does not consider them to be cost effective on larger-scale applications where the other ‘thinner' materials can easily be sprayed.
VicRoads' specification 686
VicRoads specification 686 (VicRoads 2009) details the requirements for supply and quality of materials, surface preparation, application, testing and acceptance criteria for coatings and surface treatments. Its requirements for treatments applied to improve moisture and chloride ion resistance are described in this section. Its requirements for anticarbonation coatings are not discussed in this report.
The specification allows for coatings and surface treatments to be applied to new concrete (cast in situ, or precast), or to complete repairs.
The time at which the treatment is applied varies with the substrate:
• cast-in-situ concrete and precast concrete (not steam- or heat-cured) – at least 14 days after placing
if the moisture content is less than 8%, otherwise at least 28 days after placing (the surface must be dry at the time of application)
• steam-cured concrete and concrete cured by radiant heat – at least 14 days after casting
• repairs with proprietary cementitious materials – at least 14 days after the repair is completed
• repairs with conventional concrete – at least 28 days after the repair is completed.
The requirements for materials, performance and application are as follows:
Apply protective coating systems in at least two layers.
Water absorption, measured by Initial Surface Absorption Tests (ISAT) in situ 14 days after application and curing, must not exceed 0.01ml m-2 sec-1 at 10 minutes.
The chloride diffusion co-efficient must be less than 5x10-9cm2/sec.
The dry film thickness and carbon dioxide diffusion co-efficient are also specified.
• Additional requirements for concrete located in a tidal zone:
Treatment must be formulated for application onto concrete that is dry on the outer surface but saturated internally (SSD – ‘saturated surface dry')
The system must cure between tidal cycles so that it can be immersed in seawater within three hours of application and be able to withstand hydrostatic water pressure.
The influence of surface treatments on the service lives of concrete bridges
• Additional requirements for concrete located in atmospheric and splash zones:
A dual system consisting of a pore-lining penetrant (silane) and two coats of a film-forming top coat must be applied, unless otherwise approved.
Liquid silane penetrants are to be at least 95% active and applied in two coats of at least 0.3 litres/m2 at least six hours apart.
Solid or cream silanes are to be at least 80% active and applied in one coat of at least 0.3 litres/m2.
Silane-siloxane or siloxanes are not permitted unless specifically approved.
Silane penetration depth must be at least 5mm.
Silane-siloxane or siloxane penetration depth must be at least 3mm.
Penetrants must contain a fugitive dye to assist application.
The penetrant and the film-forming topcoat must be compatible.
• With appropriate approval, pore-lining penetrants (with or without film-forming topcoats) may be
used in general applications to resist moisture ingress into concrete surfaces that do not comply with VicRoads specifications because of the presence of inactive cracks up to 0.20mm, deficient concrete cover, or excessive absorption.
• Surface treatments are not to be applied in weather conditions where wind, temperature, humidity
or rain may affect the effectiveness of the application method or the quality of the finished treatment. Temperature and humidity limits are specified.
• Surface moisture conditions at the time of application must meet the recommendations of the
treatment's manufacturer. The surface should be dry or ‘saturated surface dry'.
Specification 686 defines general methods of surface preparation and product application, and requires a trial application of at least 10m2 to check the suitability of the surface preparation and application methods. It also specifies general requirements for equipment, clean up and protection of the site, environmental requirements for the collection and disposal of waste material, handling and storage of materials and waste, and inspection. After application, an area of at least 1m2 must be tested for penetration depth, water and chloride resistance.
General VicRoads approaches
After application, the performance of treatments is not systematically monitored. The Guidelines indicate that recoating may be required after about 15 years, as indicated by the treatment beginning to allow droplet and chloride ingress. Specification 686 requires coating systems to have a guaranteed outdoor exposure life of not less than 10 years before recoating becomes necessary, although it requires coating manufacturers to provide information on repair of localised damage after five years. Ng (2006) assumes a 10-year service life for silane treatments, extending the service life of a new structure by 4–10 years.
Ng (2006) suggests that because of their toxicity and difficulty in application, silane sealants are more appropriate for new construction, rather than existing structures, particularly where they can be applied to precast components in a controlled environment. He does not recommend silane treatments
Overseas use of surface treatments
for use on existing structures because of the compliance costs associated with health and safety and environmental issues.
VicRoads prefers to emphasise good design and construction practice for new structures, rather than include surface coatings and treatments as a critical part of durability design. This is probably at least in part because of the cost of maintaining surface treatments through the life of the structure.
Ng (2006) points out that the lifetime costs of maintaining specialised systems, such as surface treatments and cathodic protection (CP), can be significant because of their toxicity (eg silane) or complexity (CP), and that such costs include not only direct maintenance costs (including logistical costs associated with assessment, maintenance and monitoring) but also indirect costs to the user relating to loss of service during maintenance. Nevertheless, he recommends applying (or at least considering applying) silane treatments to precast components as part of the durability design for new structures exposed to coastal or inland saline environments. The exception is where the risk of corrosion is high enough to justify installation of a sacrificial CP system and the structure is conveniently located for maintaining and monitoring the CP system.
3.1.7 Queensland Main Roads (QMR)
QMR has used preventive silane treatments on several structures where the depth or quality of cover was inadequate, or where cracks caused by drying shrinkage or alkali silica reaction were considered to increase moisture and chloride ingress.
Silane is considered suitable for structures that are still in reasonable condition, but it is recognised that silane treatments may not be effective if the concrete is cracked, or if the moisture content or chloride content of the concrete are high. Live cracks should be sealed, or a crack-bridging coating applied instead of a silane treatment.
Although microclimate is recognised as a significant factor in determining the corrosion risk on a particular surface (eg whether or not rain washes chlorides from the surface), the exposure conditions over the whole element also need to be considered. For example, the deck of one structure was cracked by alkali aggregate reaction. Attempts to seal the cracks failed because of large thermal movements. Silane applied to the sides and soffit acted as a tanking membrane, increasing the moisture content in the concrete and exacerbating the alkali aggregate reaction. Thus, water ingress from all surfaces must be addressed to ensure that treatment of one surface does not inadvertently trap water from other sources.
QMR prefers to manage concrete durability at the time of construction by ensuring high-quality materials and practice (including appropriate remedial work as part of a construction contract) rather than relying on surface treatments. This is because funding for capital expenditure is easier to obtain than funding for maintenance, particularly when the cost of remedying poor-quality construction is covered by the original contractor. In structures exposed to significant risk of chloride ingress, QMR now requires the reinforcement to be electrically continuous, to facilitate future corrosion monitoring and cathodic protection.
Because surface treatments are not routinely used, QMR derives its specifications from recommendations given by the manufacturers of the surface treatments.
The influence of surface treatments on the service lives of concrete bridges
3.1.8 Main Roads Western Australia (MRWA)
Most of MRWA's non-timber bridges are under 50 years old. To date, less has been spent on maintaining non-timber bridges than on timber bridges, although many non-timber bridges are now between 30 and 50 years old, so the cost of maintaining them is expected to increase (Smith and Simpson-Bint 2009). The main emerging issue for concrete bridges appears to be cracking of concrete decks caused by shrinkage and/or inadequate load capacity, rather than reinforcement corrosion, so no experience relevant to this project was reported. Little has been done to extend the service life of concrete bridges.
3.2 United Kingdom
3.2.1 BS EN 1504-2
BS EN 1504-2 covers surface protection systems for the protection and repair of concrete structures. It considers that hydrophobic impregnation (silane/siloxane) and other impregnations address three of the BS EN 1504-9 repair principles that may be used to manage reinforcement corrosion, as shown in table 3.2.
Table 3.2
Use of surface treatments as methods to address repair principles for managing reinforcement
corrosion (from BS EN 1504-2)
Principle
Hydrophobic
Other impregnation?
(as defined in BS EN 1504-9)
1: Protection against ingress
2: Moisture control
8: Increase electrical resistivity
BS EN 1504-2:2004 specifies performance characteristics, including test methods and performance requirements, for:
• hydrophobic impregnations (eg silanes or siloxanes)
• other impregnations (including film-forming organic polymers)
• surface coatings (including organic polymers, organic polymers filled with cement, or polymer-
modified hydraulic cement).
For hydrophobic impregnations, the performance characteristics include:
• penetration depth
• water absorption
• alkali resistance
• chloride ion diffusion.
Overseas use of surface treatments
For other impregnations, performance characteristics and requirements depend on the specific application for which they are being used, and include:
• abrasion resistance
• water vapour permeability
• capillary absorption and water permeability
• adhesion, with and without the influences of thermal cycling and de-icing salt
• chemical resistance
• impact resistance
• fire resistance
• slip/skid resistance
• penetration depth
• chloride diffusion.
3.2.2 England's Highways Agency (HA)
In 1986 the Highways Agency recommended impregnation of highway structures with silane, and in 1990 impregnation with undiluted iso-butyl trialkoxy silane became mandatory for structures on trunk roads. Requirements for materials used to impregnate concrete highway structures are now contained in the agency's specification for highway works, which currently specifies monomeric alkyl (isobutyl) trialkoxy silane with a minimum active content of 92% (Highways Agency 2004a). Alternative materials are accepted if they offer performance and durability that is equivalent to that of the specified silane.
In the Highways Agency's
Design manual for roads and bridges (2003)
, standard BD 43/03 covers the use of pore-lining impregnants on new concrete structures and those in service. Its Advice Note BA 85/04 (2004b) covers other coatings, including anti-carbonation coatings and waterproofing coatings, but these are beyond the scope of this investigation. BD 43/03 specifies acceptance criteria, based on drying rate, water absorption and alkali resistance, which were based on draft versions of the European standards that have subsequently become BS EN 1504-2:2004 (see section 3.2.1 above) and its related test methods.
Use of BD 43/03 was temporarily suspended for Highways Agency-managed/owned structures in July 2008, following initial results from a BRE investigation into the performance of surface impregnants. The findings and recommendations of the investigation (Calder and McKenzie 2009, see section 4 of this report) are the basis of an upcoming revision of BD 43/03, which, when complete, will align materials testing and specification requirements with European standards, including the afore-mentioned BS EN 1504 Part 2. Legal and commercial considerations are currently being ironed out prior to publication of the revised guidance. As at February 2010, the revision had not yet been published. The main change to BD 43/03 is likely to be revision of its requirements for materials, so the following points are assumed to still apply.
BD 43/03 considers that in marine environments, all exposed structural concrete elements are potentially at risk from chloride-induced corrosion and must be treated. Columns and soffits over
The influence of surface treatments on the service lives of concrete bridges
brackish water must also be treated. For structures in other environments, it recommends treatment of all reinforced and prestressed concrete surfaces subjected to de-icing salt spray and/or possible leakage from deck joints.
BD 43/03 requires that new structures be impregnated before being put into service.
BD 43/03 requires that structures already in service that have not been treated previously shall be treated if they comply with certain criteria (see below). It offers limited guidance on how to decide when to treat a structure in service, that decision being made by the Overseeing Organisation in consultation with the Maintenance Organisation on the basis of an economic evaluation (see below). It notes that normal practice is to apply a surface treatment in association with other planned maintenance, although on some structures, surface treatments have been applied under separate contracts.
BD 43/03 requires that impregnation be carried out only on elements in which the reinforcement is not corroding. Therefore, structural elements to be treated must be free from rust staining, cracking, delamination and spalling. If defects are present, repairs may be necessary prior to the surface treatment. Thus a site investigation is needed to determine whether surface treatment is necessary.
The simplest form of site investigation is a visual assessment, supplemented with hammer tapping to detect delamination. BD 43/03 Appendix A describes a more detailed testing regime used in England, whereby the decision to apply a surface treatment is based on measurements of half-cell corrosion potentials, and the need for ongoing monitoring after treatment is determined from measurements of chloride ion contents. If the corrosion potential indicates that corrosion is unlikely, then the element may be treated. If the chloride ion content exceeds the specified limit, then half-cell potentials must be monitored in the future as part of the six-yearly Principal Inspections to identify significant changes.
BD 43/03 recommends that the site testing (and ongoing monitoring, if required) be carried out during Principal Inspections.
BD 43/03 notes that few structures less than 10 years old (ie post-1990) would not have been treated, and that the condition of concrete in these structures is assumed to be good, with low concentrations of chloride at the reinforcement. Site testing of such structures built since 1990 is not necessary prior to surface treatment, unless they show signs of rust staining, cracking and spalling.
Prestressed or precast elements do not need to be tested before treatment. (A Highways Agency representative advised that in general, precast/prestressed units are considered to be denser than reinforced concrete sections and less vulnerable to chloride ingress. He said that HA considers it inadvisable to embark on wholesale intrusive testing, although if cause for concern is indicated on a particular structure, it would be investigated and if necessary, considered for treatment).
For all other elements more than 10 years old (ie built before 1990) that have not previously been treated, the need for a surface treatment must be determined by a site examination.
In practice, the Managing Agent decides whether to treat an in-service structure based on economic evaluation in accordance with the Highways Agency's
Value management of the structures renewal programme (2009). This procedure adopts an holistic approach to structure maintenance/renewal, and uses a scoring system to rank schemes in terms of value based on likelihood and consequences of risks to safety, functionality, sustainability and the environment. It recognises that impregnation is a special case and is time-critical. It therefore recommends prioritisation, which is fed into the equation by assuming high sustainability consequences. Nevertheless, impregnation is considered as preventive
Overseas use of surface treatments
maintenance and, as such, rarely scores highly enough to be funded unless undertaken at the same time as other maintenance, such as replacement of waterproofing, surfacing, or expansion joints.
Jandu (2008) summarises the process by which the Highways Agency selects the projects it will undertake. He identifes the limitations of the scoring system used to prioritise projects, including its subjective element, and stresses that although final decisions take into account the outcome of the prioritisation process, they also take into account regional, political and social issues/constraints that may override the outcome of the analytical process. Consequently, surface treatments may rarely have been applied in practice, despite the requirements of BD 43/03. This may explain the limited practical experience reported in section 3.2.3.
Use of hydrophobic pore liners in the UK has, to date, largely been limited to iso-butyl trialkoxy silane, as originally specified by the
Specification for highway works (Highways Agency 2004a), which allows Overseeing Organisations to accept alternative materials that demonstrate suitable durability and performance. BS EN 1504-2:2004 introduced specific requirements for surface-protection systems based on standardised test methods, and the Highways Agency anticipated that this would allow other types of impregnants to be used, particularly other types of silanes and siloxanes. One product that blocks pores with hygroscopic crystals has been accepted for use, following tests that showed it complied with BD 43/03 requirements; however, as mentioned previously, use of all materials is currently under review, following the temporary suspension of the standard.
BD 43/03 refers to the potential difficulty of treating surfaces that have been membrane-cured (particularly with silicate-based products) or previously treated. Opus staff who have experience of bridge maintenance in the UK reported needing to steam clean a new surface to remove residues of curing membrane.
The UK Department for Transport's
Management of highway structures (2005) states that surface impregnation is unlikely to have significant benefit on concrete already moderately or heavily contaminated with chlorides and where the steel has started to corrode (also see section 4.5 of this report), but that it should be considered as a proactive preventive measure after removal of chlorides by, for example, patch repair.
BD 43/03 states that impregnation using monomeric alkyl (isobutyl)-trialkoxy silane is known from research evidence to be highly effective for at least 15 years if applied correctly, and provided it is not subjected to physical abrasion or degradation mechanisms. As a longer service life is anticipated, it suggests assuming that until further experience with this treatment is amassed, reapplication would be required after 20 years.
Retreatment is considered necessary when ongoing monitoring of half-cell corrosion potentials indicate a significant change in corrosion potential, and when critical levels are reached over a significant area of the element. It stresses the need to ensure that subsequent treatments are compatible with the preceding treatment.
The influence of surface treatments on the service lives of concrete bridges
3.2.3 Experience of maintaining agents
Calder et al (2006) recently surveyed the Maintaining Agents of the 14 geographic Trunk Road Maintenance Areas in England to assess the extent and effectiveness of treating bridges built since 1990 and older in-service bridges. Their principal findings were as follows:
• Most of the agents considered impregnation to be an effective method of improving concrete
durability, although concerns were raised about the health risks involved with application of alcohol-based solutions.
• BD 43/03 (and its predecessors) have generally been followed for new construction, repairs and
remedial work, but it is unlikely that many in-service structures have been treated as a preventive measure. None of the agents reported treating in-service structures routinely.
• Some of the agents reported operational difficulties associated with health and safety and weather
issues (anecdotal evidence from Opus staff supports this observation).
• Only nine of the agents had information about which bridges had been treated, and eight agents
claimed to have details of the treatments.
• Half of the agents had pre-/post-monitoring data.
Two agents were questioned in more detail about their use of surface impregnations:
• One reported that about 30% of pre-1990 structures, and over 90% of post-1990 structures had
been treated. Just over a third of the treated pre-1990 structures were 30–40 years old when treated, probably reflecting the large number of bridges built in the 1960s; the rest were younger. Only five structures had been retreated, after 4–10 years. Monitoring programmes were in place for many of the agency's structures.
• The other agent reported that 11% of pre-1990 structures had been treated. They were up to 30
years old when treated. The agent did not say whether the others had been treated and did not provide information on newer structures.
At least one agent reported that within the Highways Agency's
Value management of the structures renewal programme (2009), it was difficult to obtain a high enough score to treat vulnerable structures. None reported having an ongoing programme for impregnation of existing structures. Others reported being limited by financial restrictions. Impregnations appeared to be limited to just a few isolated structures each year, carried out as part of other remedial works.
Most of the products applied were isobutyl trialkoxy silanes, in accordance with Highways Agency requirements.
Calder et al (2006) did not analyse the monitoring data as part of the project, but recommended that this be done to demonstrate the effectiveness of impregnation in improving durability. Their findings indicated that information on the impregnation of structures was not collected or stored systematically between or within agencies (including between successive agents within a particular area) and that even where information was available, it would be difficult to retrieve and analyse.
3 Area 11 was subsequently absorbed into Areas 7 and 9 and hence there are now only 13 areas.
Overseas use of surface treatments
Pearson and Cuninghame (1998) noted some scepticism amongst engineers about the effectiveness of silane, and about its cost effectiveness when compared to cheaper materials. They also noted a widespread belief that the application of silane is difficult to control and check. BD 43/03 provides for quality control of the product used during the application process to ensure that the product complies with requirements. The need to test for the quality of application was borne out by anecdotal evidence from an engineer with UK bridge maintenance experience, who noted that the silane looked and behaved like water when it was being applied, and that simply observing the application process was not sufficient to assess the quality of material and application.
Very little of England's trunk road network is situated in a marine or coastal environment. The two agents who responded in more detail to the TRL survey covered areas where all of the trunk road structures were inland. Experience of hydrophobic impregnation of England's trunk road structures therefore relates predominately to inland structures, which are affected by de-icing salts used to keep roads free of ice in the winter, rather than to structures exposed to chlorides from a marine environment.
3.2.4 Wales and Scotland
The Welsh Assembly Government and Transport Scotland, as trunk road agencies for Wales and Scotland, have respectively adopted the guidance of BD 43/03 and its predecessors without amendment. Despite the present ban on all impregnation in England (because of the temporary suspension of BD 43/03), the trunk road agencies of Wales and Scotland still allow surface treatments of new trunk road structures, although the proposed materials are assessed individually for each case with due regard to the findings of recent research.
Neither agency has a formal programme of treating in-service structures. Surface treatments are usually applied in conjunction with other major maintenance activities, or following concrete repairs and the like, although in principle they may be applied as a separate activity.
3.3.1 New Brunswick Department of Transportation (NBDoT)
NBDoT does not routinely use surface treatments such as silanes to increase the service life of concrete beams, although they have been occasionally used as a ‘last resort, to avoid having to remove concrete'. This may be because in New Brunswick, concrete beams are used on smaller structures, where the cost of replacement (and therefore the cost difference between repair and replacement) is less than on a large bridge. It also reflects the more significant issues associated with salt contamination in the tidal zone and from de-icing salts, neither of which can be addressed by surface sealers.
NBDoT does not have a specific methodology for determining the effectiveness of surface treatments, but does use concrete deterioration modelling to estimate service life in the durability design of new bridges. The correspondent observed that in some cases the [life cycle cost] analysis to determine the benefits of a preventive treatment may cost more than the actual treatment/repair, and questioned whether the models used were sufficiently inclusive.
The influence of surface treatments on the service lives of concrete bridges
For new concrete construction, NBDoT specifies calcium nitrite corrosion inhibitor, a low water to cement ratio, and supplementary cementitious materials. Silane treatments may be used in addition to these but are not to be used as a substitute.
3.3.2 Alberta Infrastructure and Transportation (Alberta Transportation)
Alberta Transportation has been sealing bridge decks with silanes and siloxanes since 1986 to prevent moisture and salt being absorbed by the concrete, and to prevent water leakage through cracks or joints (Alberta Transportation 2008). Precast beams have been sealed with epoxy or acrylic sealers since the mid-1970s.
Exposed trafficked surfaces (decks and overlays) are sealed with 100% silane shortly after construction. Subsequently they are retreated with 40% silane on a four-year cycle for major highways, and a longer cycle for lower-volume highways, which are exposed to less frequent applications of de-icing salt. The four-year cycle is based on abrasion tests that relate the depth of sealer penetration to depth of abrasion. From 2010, 100% silane products will probably be used to meet more stringent requirements for volatile organic compounds (VOCs). These may enable extension of the maintenance cycle to six years.
Film-forming acrylic sealers are specified for non-trafficked surfaces (kerbs and barriers) because initially they were cheaper, gave similar performance to the penetrating sealers, and it was easier to ensure the desired coverage rate on vertical surfaces because of their higher viscosity. In addition, staff were originally unsure about the performance of silane because they couldn't see the material on the concrete surface. However, some agencies use penetrating sealers on kerbs and barriers.
The annual bridge deck maintenance programme involves washing every bridge deck once a year. The risk of corrosion on each bridge over 35 years old is monitored every four, six, eight or 10 years as appropriate for the volume of traffic/application of de-icing salt. Corrosion monitoring includes measuring half-cell corrosion potentials and chloride contents, along with delamination surveys and a detailed visual inspection. Chloride contents are usually only measured when half-cell corrosion potentials indicate an increased risk of corrosion – the chloride contents are then used to help identify the cause of the high potentials. They are also used to identify the amount of de-icing salt that has been applied and the extent of chloride contamination. Trends in these parameters, observed over multiple cycles, have allowed the development of models for predicting when rehabilitation is required.
Different contractors and consultants are used for sealing and monitoring. To avoid the cost and inconvenience of having to coordinate the two operations, they are conducted independently, sealing being completed regardless of testing, as it is considered the cheapest form of preventive maintenance. The corrosion-monitoring cycle is adjusted as necessary so that the effectiveness of repairs can be measured. For example, if a deck is to be repaired in a scheduled testing year, then the monitoring may be delayed for two years and then put back onto a regular four-year cycle.
Alberta Transportation's
Specification for concrete sealers (2009) and
Best practice guidelines (2008) define five types of product for different applications:
• Type 1– penetrating sealer for trafficked surfaces
Type 1a: ‘silane sealer' sealer with solids content 14–32% – for sheltered conditions; concrete
moisture content (relative humidity) up to 55%; concrete older than 28 days
Overseas use of surface treatments
Type 1b: ‘40% silane sealer' with sealer solids content 25–33% – for outdoor conditions;
concrete moisture content (relative humidity) up to 70%; concrete older than 28 days; may be used as a primer for type 2b sealers on badly scaled surfaces if the specific products are compatible
Type 1c: ‘100% silane sealer' with sealer solids content 65–72%, low VOC – for outdoor
conditions; new concrete (including steam-cured precast concrete) with a water to cement ratio of less than 0.45 and concrete moisture content (relative humidity) up to 80%
• Type 2 – clear, film-forming sealer for non-trafficked surfaces
Type 2a: single-component product – for concrete moisture content up to 70%; less-
experienced applicators; concrete older than 28 days
Type 2b: two- or multi-component epoxy product – for concrete moisture content up to 70%;
experienced applicators; concrete older than 28 days
• Type 3: pigmented film-forming products – for exposed elements where aesthetics are important;
concrete moisture content up to 70%; concrete older than 28 days.
Performance requirements for the sealers are based on waterproofing ability, water vapour transmission, alkali resistance (type 1 sealers), hiding power and colour (type 3 sealers), ease of use, and volatile organic compound content (for type 1c sealers). Specific test methods are prescribed for measuring these properties. Individual products are approved by Alberta Transportation for up to five years on the basis of test results for these properties. Approved products are listed on Alberta Transportation's website. A product must be resubmitted for approval if its formulation changes.
Alberta Transportation's 2007 specification for cast-in-place concrete bridge construction requires a type 1c sealer to be applied to all concrete surfaces that are susceptible to deterioration by water and de-icing salt. This includes all surfaces to 600mm below grade or the lowest water level, faces of end diaphragms nearest the abutment backwall, the inside face of the abutment backwall, and the top surface of the abutment seat (excluding bearing recess pockets), but does not include the underside of bridge decks, concrete diaphragms in interior bays, or surfaces protected by other materials.
3.3.3 South Carolina Department of Transportation (SCDOT)
SCDOT allows iso-butyl trimethoxy, n-octyl trimethoxy and iso-octyl trimethoxy silanes to be used on bridge decks (SCDOT 2007). They must be 40% silane by weight and may contain a fugitive dye.
SCDOT (2007) requires treatments to penetrate at least 4mm into the concrete surface, make it non-wettable, and not change its colour or friction properties. It also specifies requirements for moisture vapour transmission, chloride ion resistance and weathering resistance. SCDOT prequalifies individual products based on these requirements.
3.4 Overall impressions from overseas experience
The agencies contacted in the course of this research all acknowledged the potential benefits offered by surface treatments, particularly silane/siloxanes, and most permitted, encouraged or required their use on existing structures where appropriate. For new structures, most of the agencies preferred to
The influence of surface treatments on the service lives of concrete bridges
address durability issues by managing concrete and construction quality, rather than by applying surface treatments to new concrete.
Analyses of life cycle costs and benefits of treatment were acknowledged as expensive and time consuming, and the findings could be overridden by social or political needs. Several sources expressed the need for a risk- or value-based approach, based on a mixture of analytical techniques and experience, for determining the need for treatment. This approach would take into account the age and/or condition of the bridge, treatment application costs, measured chloride ion profiles, and the potential benefits of the treatment as indicated by its effects on chloride contamination and moisture content of the concrete. As access is a major component of the cost of treatment, readily accessible elements may be treated without the detailed analysis required to justify treating a bridge where access costs are significant. To reduce access costs, the treatment may be applied when access is provided for other maintenance activities, although extra costs may be incurred in coordinating separate contracts.
The performance of a surface treatment is strongly influenced by the specific composition of the particular product. Thus the agencies contacted and specifications reviewed tended to specify treatments by composition as well as performance, and some also required products to be preapproved.
Application protocols aimed to achieve maximum performance from the treatments by requiring that the concrete substrate be relatively dry when treated.
Agencies also recognised that surface treatments have a limited life, and therefore provided for reapplication at regular intervals. The need for reapplication was determined by a visible reduction in water repellency and/or decreasing half-cell corrosion potentials. The maximum estimate of life for a treatment was 20 years.
3.4.1 Barriers to the use of silane/siloxane surface treatments
Because of environmental and health/safety concerns, silane/siloxane surface treatments have not been used as widely as might be expected for preventing or delaying the onset of reinforcement corrosion in bridges. These problems may be overcome by the recent introduction of products that are supplied as creams or gels. These products may also make it easier to achieve satisfactory impregnation depth because the active ingredient does not evaporate or drain away during application.
Another barrier to their uptake is the difficulty of detecting the quality and consistency of product and application by visual inspection alone. Thus specifications include requirements for material properties and performance properties, to ensure that the quality of the product and its application are satisfactory and consistent.
A third barrier is the uncertainty over what the acceptance criteria should be. Although silicate-based treatments were admitted for use by the Highways Agency in the early 2000s, on the basis of products meeting performance requirements, they are not widely accepted or used by the road-controlling authorities contacted. The recent withdrawal of the UK document that covers their use, even though only temporary, indicates that doubt remains about how to specify acceptance criteria that reliably distinguish between acceptable and non-acceptable products. This suggests that until the benefits and limitations of this type of treatment are better understood, their use should be limited to trials where they will be compared to other treatments, including ‘no treatment', or to applications where the risk of poor performance is acceptable.
Performance of surface treatments
Performance of surface treatments
4.1 Evaluating surface treatments for use on
New Zealand bridges
The focus of this project is the use of surface treatments to prevent or slow the rate of corrosion of reinforcing and prestressing steel in beams and other superstructure elements that are exposed to seawater splash or spray. Much of the literature data on the performance of surface treatments relates to their use on trafficked surfaces, where longevity of performance is determined by the penetration depth of the treatment relative to the rate at which the surface is abraded. Other reports relate to performance on surfaces exposed to ponding or tidal conditions. These aspects are not an issue for the concrete surfaces of interest in this investigation, ie those exposed to seawater splash and spray. Nevertheless they are considered here because they represent the majority of applications internationally and therefore are the subject of significantly more research than the application of surface treatments to structures in coastal environments.
Although this report summarises the findings of independent investigations reported in the technical literature, it does not purport to be a complete literature review. It does not consider information provided by suppliers of surface treatments for two reasons: firstly, because it was not practical to evaluate information from all suppliers; and secondly, to avoid appearing to advertise or endorse (or otherwise) particular products.
The performance of surface treatments designed to reduce the risk of chloride-induced corrosion on concrete exposed to seaspray or splash can be assessed by measuring the depth of penetration of the treatment, the water absorption of a treated surface, and the uptake of chlorides through a treated surface. The durability of the treatment (ie how long it remains effective) can be determined by measuring its performance before and after exposure to, for example, alkali (as in APAS 01608) or, for trafficked surfaces, abrasion (not applicable to the applications considered here).
The difficulty of testing surface treatments in a way that represents widely varying in-service conditions is well known. In particular, performance will be determined by concrete quality (the water to cement ratio and cementitious binder content) and the moisture content of the concrete both when the treatment is applied and at the start of the test. Consequently, many different test methods are used by researchers and road-controlling authorities. The issues associated with testing were highlighted in a recent investigation reported by Calder and McKenzie (2009), which resulted in the temporary withdrawal of a UK national policy document while issues relating to testing and specification are being resolved.
The acceptance criteria determined for one particular test method cannot be applied to the results from another test method that measures the same property. Therefore the criteria used by one agency should not be adopted by another unless the properties can be measured in accordance with the specified standards.
The acceptance criteria used by a particular agency may have been determined for a particular concrete. For example, VicRoads specification 686 (2009) requirements are intended for the concrete mix design specified by VicRoads specification 610 (2009) for bridgeworks, and APAS 0168 (2009) requirements are based on concrete with a water to cement ratio of 0.40 (indicative compressive
The influence of surface treatments on the service lives of concrete bridges
strength 51MPa, indicative dry density 2380kg/m3, and indicative chloride ion content <0.2% by mass of concrete). Such acceptance criteria may not be appropriate for concretes of significantly better or poorer quality.
If a particular product's performance has been shown to comply with the requirements of at least one bridge asset owner, it will probably perform satisfactorily on New Zealand bridges. A product of unknown performance, but with a composition accepted by at least one bridge owner, will probably also perform satisfactorily. Nevertheless, in both these situations the supplier should certify that the chemical composition and the concentration of the active ingredient in the product to be supplied for the particular contract are the same as those of the product that was accepted by the other agency.
Similarly, if a particular product has no history of acceptance by another bridge asset owner, then the supplier should provide details of the product's chemical composition and the concentration of the active ingredient. It may be considered if its composition and concentration meet the requirements of APAS or other existing specifications, but its potential performance should be evaluated before application.
The effectiveness of a surface treatment is determined not only by the particular product used, but also by the method of application and the condition of the surface to which it is applied. Therefore the effectiveness of a surface treatment should be evaluated after application as part of the acceptance criteria for the particular contract, irrespective of whether a product has been accepted by another agency or previously used on a New Zealand state highway structure.
The most practical performance tests are those that measure penetration depth and/or water resistance, although Calder and McKenzie (2009) suggest that measurement of chloride ion resistance may be a more accurate indicator of performance. Performance should be evaluated using test methods and associated acceptance criteria cited by existing specifications.
The following sections summarise selected literature reports of the performance of relevant surface treatments.
4.2 Penetration depth
Examples of penetration depths specified by various agencies are presented in appendix A, table A1.
Attanayake et al (2006) consider that penetration depth determines the effectiveness and the durability of penetrating sealers used on bridge decks. They point out that the depth of penetration achieved in a particular application is determined by:
• the properties of the sealer – viscosity, molecular size and weight, surface tension and affinity for
• the properties of the concrete – pore size distribution and tortuosity, pore surface topology, crack
width and density, and moisture content
• the environmental conditions – temperature, humidity, application pressure and sealer's reactivity.
For a given sealer and concrete, they consider that the depth of penetration of the sealer is determined by the moisture condition of the outer 6mm of concrete when the sealer is applied, and provide a method to estimate the drying period required between surface preparation (by water blasting) and
Performance of surface treatments
sealer application. They suggest that relatively impermeable concretes may be more expensive to treat, because extra material is required to replace liquid sealer that evaporates or drains from the surface during the prolonged ‘ponding time' required to achieve a specified penetration depth.
McGettigan (1992) argued that simply measuring the depth of the non-wettable band on a cross section of treated concrete could be misleading because the water repellancy may, in practice, decrease significantly within the depth of apparent penetration. He considers the critical property to be ‘depth of penetration over which water repellancy is consistent', and that comparison of the water absorption of a treated specimen before and after abrasion (see section 4.3) is a better measure of performance than ‘penetration depth indicated by visible water repellancy'.
Manufacturers may add other components, such as wetting agents or viscosity modifiers, to their products to aid penetration. This does not necessarily improve their water resistance.
Suppliers of surface treatments often quote penetration depths achieved in site applications to demonstrate the effectiveness of their products. McGettigan's comments (above) suggest that penetration depth alone should not be the basis for selecting a surface treatment unless no other performance data is available, which is why many authorities use measurements of water uptake instead (see section 4.3).
Calder and McKenzie (2009) attempted to measure the penetration depth of core samples from treated and untreated surfaces, but were unable to detect a water-repellent strip near the surface of concretes treated with silane/siloxane or silicate-based treatments.
Raupach and Wolff (2005) found that penetration depths were greater for a solvent-based cream (with 80% active ingredient) and a solvent-free liquid (with 98–100% active ingredient), than for solvent-free products with 20–40% active ingredient. The two dilute products were water-based, and the polarity of the water (which reduces its wetting ability compared with a non-polar solvent) was considered to have reduced their penetration. Penetration depths were also greater for 15MPa ‘poor-quality' concrete than for 25MPa concrete. After one year of exposure to natural and accelerated weathering, the concrete's ability to dry was influenced more by the treatment's application rate than by penetration depth alone.
Nevertheless, measurements of penetration depth have been used to explain other observed performance characteristics:
• Dai et al (2010) carried out exposure site trials using laboratory-cast specimens and proprietary
silane, silane-siloxane and silicate-based surface treatments. To produce results in a practical time frame, they used lower-quality concrete (cement content 248kg/m3, water to cement ratio 0.68) than would normally be used on bridges in New Zealand. They found that significantly greater penetration depths (as measured by water repellence of a split specimen) were achieved with a silane gel and a silane cream, compared with silane liquid and silane-siloxane liquid, and that penetration depth affected subsequent chloride ion penetration and corrosion activity (see sections 4.5 and 4.6). Sodium silicate treatments did not produce a water-repellent surface layer. Dai et al point out that sufficient depth of penetration is necessary to overcome variations in the microstructure of a surface that would locally increase ingress of chlorides and moisture, and that the risk of such ‘leakage' needs to be considered on a statistical basis when determining penetration depth requirements.
• Weyers et al (1995) take penetration depth and ‘leakage' of chlorides into account when modelling
the service life of surface treatments (and of treated concrete).
The influence of surface treatments on the service lives of concrete bridges
4.3 Effect on water absorption/vapour permeability
Examples of water absorption and water vapour permeability characteristics specified by various agencies are presented in appendix A, tables A2 and A3 respectively.
Silane sealers can reduce water absorption by at least 82% (Alberta Transportation 2009), and can reduce internal relative humidity (RH) from 50–80%RH to 30–40%RH (Alberta Transportation 2008).
Darby et al (1996) carried out laboratory tests and in-situ tests on pier crossheads exposed to ponding and run-off from the bridge deck. Laboratory tests showed that silane treatments significantly reduced capillary absorption and resistance to water vapour diffusion. In-situ monitoring showed that silane treatments significantly reduced water absorption. Electrical resistivity gradually increased as a result of the drying.
Calder and McKenzie (2009) measured the weight gain (‘sorptivity') of treated and untreated concrete cubes (360kg/m3, water to cement ratio 0.45) exposed to water on one surface for up to seven days. Silane/siloxane treatments all significantly reduced the uptake of water. Silicate and siliconate treatments resulted in similar, or slightly higher, water uptake than untreated controls, even though these products complied with the requirements of BD 43/03.
Calder and McKenzie (2009) also tested cores taken from three bridges where surface treatments had been applied either to new concrete (two structures) or 35 years after construction. The cores from one structure showed little difference in sorptivity between untreated surfaces and surfaces that had been treated with a silicate-based product. Cores from the structure treated with silane/siloxane recorded slightly lower sorptivity than either of those from concrete treated with silicate. The differences in sorptivities were not related to differences in moisture contents at the time of application. Water droplets placed on a surface treated with silane/siloxane took longer to be absorbed than droplets on an untreated surface or either of two surfaces treated with silicate-based products. The authors concluded that the results of surface absorption tests on site or laboratory samples could be significantly affected by the condition (roughness) of the surface at the time of treatment or testing. They recommended that chloride ingress may be a more appropriate measure of the effectiveness of surface treatments, but noted that such methods are more expensive and generally not practical.
Laboratory and exposure site trials by Raupach and Wolff (2005) showed that the water resistance and breathability of concrete treated with four different silane/siloxane products improved with higher application rates. The ability of the treated concrete to dry was influenced more by application rate than by concentration of active ingredient or penetration depth. The standard application rates used in the tests were less effective for 15MPa concrete than for 25MPa concrete, indicating that higher application rates are need for more permeable surfaces.
Exposure site trials reported by Dai et al (2010) found that silane and silane-siloxane treatments significantly reduced water absorption during one year of exposure to cyclic salt spray. The silicate treatments were much less effective. Water resistance was closely related to penetration depth. The silanes applied as cream or gel were the most effective, providing effective barriers even when the concrete cracked after impregnation.
Performance of surface treatments
When concrete is partly dry, air can enter the pores in the hydrated cement. Partly dry concrete also contains enough liquid water to dissolve atmospheric carbon dioxide and calcium hydroxide from the hydrated cement, thereby allowing them to react to form calcium carbonate. Carbonation rates are maximised at a relative humidity of 60–80% in the concrete pores.
Depending on the moisture content of the concrete when they are applied, surface treatments that reduce moisture ingress but are not a vapour barrier may lower the moisture content of the concrete to a level where carbonation rates increase. This was demonstrated by Ho and Ritchie (1992) who compared two unidentified ‘coatings'. Both were applied to new concrete and were shown to remain effective as water barriers for at least three years. Compared to the uncoated references, one product, with a penetration depth of 1mm, reduced carbonation significantly; the other, with a penetration depth of 5mm, significantly increased carbonation.
Ibrahim et al (1999) found that after five weeks in a saturated carbon dioxide environment, concrete specimens (water to cement ratio 0.45, cement content 350kg/m3) treated with silane or silane-siloxane were carbonated to greater depth than specimens treated with sodium silicate. No carbonation was detected in specimens coated with an acrylic membrane, or in specimens treated with a silane-siloxane with an acrylic topcoat.
The Concrete Society (1997) comments that polymerisation of a silane/siloxane may take longer than usual on carbonated or very dry concrete. The use of treatments applied as creams or gels should, in most cases, minimise the problem of the treatment evaporating before it's had time to react, but their effectiveness on deeply carbonated concrete is uncertain. Attanayake et al (2006) refer to the need to remove carbonated concrete before treatment.
An increase in carbonation rate will reduce the time to corrosion initiation, although the subsequent rate of corrosion may increase or decrease depending on the concrete's moisture content.
Severe or extensive reinforcement corrosion caused by carbonation alone is not as common in New Zealand bridges as the ingress of moisture and chloride ions.
Nevertheless, carbonation produces changes in the chemistry of hydrated cement. These changes result in the release of chloride ions that would otherwise be chemically bound within the uncarbonated hydrated cement and therefore unable to contribute to corrosion. Thus carbonation may increase the risk of chloride-induced corrosion if the concrete contains chloride-based accelerating admixtures or is exposed to external sources of chlorides.
Therefore the effect of a surface treatment on carbonation needs to be considered not only in terms of its effect on carbonation-induced corrosion, but also on the distribution of chlorides that may be present in the cover concrete. Application of an anti-carbonation coating such as an acrylic membrane may be beneficial where the quality and/or depth of cover concrete provides insufficient protection from the ingress of moisture and air, or where carbonation may increase the risk of chloride-induced corrosion.
The influence of surface treatments on the service lives of concrete bridges
4.5 Effect on chloride ingress
Examples of chloride ingress characteristics specified by various agencies are presented in appendix A, table A4.
Ibrahim et al (1999) found that the chloride ion resistance of a good-quality concrete immersed in a chloride solution was improved by silane and silane-siloxane treatments, particularly when the latter was overcoated with an acrylic membrane. Sodium silicate treatments were less effective.
Sandeford et al (2009) described the findings of extensive inspection and testing that was carried out on several wharves as part of an ongoing corrosion management programme for a port owner. The deck soffit of one of the wharves, which was 11 years old at the time of the investigation, had been treated with silane. The test results were variable and the authors suggested this might be ‘a result of inconsistent application and possibly application of silane some time after construction'. Nevertheless the authors considered that silane significantly reduced surface chloride contents.
Laboratory ponding tests reported by Calder and McKenzie (2009) found that the eight silane/siloxane treatments tested all reduced chloride ingress into concrete (360kg/m3, water to cement ratio 0.45) by 80–98%. In contrast, silicate-based pore-blocking treatments reduced chloride ion ingress by less than 25%, despite meeting BD 43/03 requirements. On the basis of ponding tests and sorptivity tests (see section 4.3 of this report), they recommended that the use of ‘crystal growth' pore blockers for highway structures be reviewed, that further information be obtained about the reactions that such pore-blockers undergo, and that the approval testing of the particular products concerned be repeated.
Vassie and Calder (1999) and Calder (2002) reported the findings from ongoing monitoring of chloride ingress during the 15 years after the application of a trial silane treatment on piers of a UK highway bridge. The bridge was one year old when treated and the silane was applied at a similar dosage to that now specified by BD 43/03, although the period between coats was shorter than the period now specified. The results showed that silane treatment significantly reduced chloride ingress: at all positions on the piers, the chloride contents at 10mm from the treated surface were less than the value considered to be a threshold for corrosion initiation; but in untreated concrete, chloride contents exceeded this value to a depth of 20–25mm. Although the pier was exposed to spray from a road surface that had been treated with de-icing salt, rather than to seawater or seaspray, the mechanism of exposure, ie splashing and spray, may be considered similar to that experienced by elements in the splash and atmospheric zones on a marine structure.
McCarter et al (2008) and Nanukuttan et al (2008) reported the findings from ongoing monitoring of chloride contents on concrete samples simulating pier stems in a range of marine environments, including tidal exposure, high-tide level, exposure to splash above the high-tide mark, and exposure to airborne spray. One set of samples was treated with a proprietary alkyl alkoxy silane in accordance with the UK Highways Agency's specification BD 27/86, which has similar requirements to BD 43/03. After seven years, the difference between chloride ion profiles in treated and untreated samples indicated that the effectiveness of the silane treatment was highly sensitive to exposure and time. It did not reduce chloride ion ingress in tidal or submerged exposure, but did reduce chloride ingress in concrete exposed to splash, particularly up to 1.5m above high-tide level. During the first year of the experiment it reduced chloride ingress in the splash and atmospheric zones, but after seven years the effect was minimal. This may reflect the durability of the treatment (see section 4.7).
Performance of surface treatments
It is possible that in the project described above, the high cement content (460kg/m3) and low water to cement ratio (0.4) of the concrete, and the extended curing of the samples, resulted in inadequate penetration of the silane treatment. CIRIA (1987) noted that although penetration depths of 2–4mm into high-quality concrete were claimed for the most commonly used silane, penetration into well-cured surfaces of concrete with a low water to cement ratio were seldom more than 1mm unless the surface was carefully prepared and dry before treatment. Many specifications now detail drying and cleaning procedures prior to the treatment of a surface, to ensure that adequate penetration depths are achieved.
Dai et al (2010) found that silane treatments applied as cream, gel or liquid had significantly reduced chloride ion ingress from salt spray after one year. The silane-siloxane liquid product was less effective than the silanes. The silicate treatments did not reduce chloride ingress even when overcoated with an acrylic resin. These observations were directly related to the penetration depths of the treatments (see section 4.2). They also observed that chloride penetration depth varied in individual specimens because of variations in concrete microstructure, and noted that relatively deep overall penetration is needed to avoid localised ‘chloride breakthrough' at more permeable locations.
The Concrete Society (1997) notes that most surface treatments reduce water absorption, but that some treatments allow the concrete to dry more than others. It observes that drier concrete generally has a higher electrical resistivity, thus reducing the rate of any ongoing corrosion; but that where water can ‘wick' from sources other than the treated surface, soluble salts may concentrate at or near the treated surface, which may cause visible efflorescence or surface scaling/spalling. It states that absorption of solutions into concrete is the most rapid, and therefore the most common, means of transporting chlorides into the concrete; and that once in the concrete, chlorides are transported by diffusion within the pore water. The Concrete Society considers that although diffusion is a slower process than absorption, and is complicated by interactions with hydrated cement, treatments stopping further ingress will have little effect on the diffusion process and therefore corrosion will eventually occur if the chloride ion concentration is high enough. Nevertheless, surface treatments could conceivably reduce diffusion rates if they allow the concrete to dry sufficiently. This is more likely in concrete with a relatively open-pore structure and less likely in concrete with a low water to cement ratio.
4.6 Effect on corrosion activity
The concepts of corrosion initiation and corrosion propagation discussed in this and the following sections are described in appendix B.
Reducing the moisture content and chloride content of the concrete should delay the onset of corrosion, and should reduce corrosion rates if corrosion has already been initiated when the surface treatment is applied.
To evaluate the performance of surface treatments on rebar corrosion in partly immersed/buried columns of a structure, Ibrahim et al (1999) treated the ‘above ground' surfaces of partly immersed reinforced concrete specimens (water to cement ratio 0.45, cement content 350kg/m3) in which reinforcement corrosion had been initiated prior to surface treatment. They found that silane and silane-siloxane treatments reduced half-cell corrosion potentials and corrosion current densities, but that treating the surface with sodium silicate had little effect. The greatest overall protection was achieved with silane-siloxane overcoated with an acrylic topcoat. The authors attributed the results to
The influence of surface treatments on the service lives of concrete bridges
reduced oxygen and moisture diffusion, and concluded that the silane and silane-siloxane treatments (and acrylic coatings) could be used to rehabilitate structures in which corrosion had commenced.
In-situ tests carried out by Darby et al (1996) on pier crossheads found that silane treatments reduced seasonal and other short-term effects on half-cell corrosion potentials and electrical resistivity. Corrosion potentials gradually became more positive and electrical resistivity gradually increased. Limited measurements of corrosion current showed that silane treatment reduced the risk of corrosion within and away from repaired concrete, and reduced the rate of development of an incipient anode immediately adjacent to a patch repair but did not prevent it.
Calder (2006) reported the interim findings from laboratory tests that aimed to ascertain whether silane treatment reduces chloride-induced corrosion if the treatment was applied after corrosion had started. Concretes with water to cement ratios 0.50 and 0.65 were tested. After eight years, half-cell corrosion potentials in the treated specimens were more positive than those in the untreated controls, and corrosion rates were significantly lower for the treated specimens than for the untreated controls. One untreated specimen had cracked after six years.
In a study of the effects of silane admixtures (as opposed to surface treatments), Titarelli and Moriconi (2008) found that steel corroded faster in cracked concrete containing silane admixture than in cracked concrete not containing the silane admixture. This behaviour was attributed to oxygen being able to diffuse faster through the partly dry pores to the cathodic sites on the reinforcement, with anodic sites being created at the cracks. In contrast, silane admixtures reduced corrosion in uncracked concrete by reducing water and chloride ingress. Two mix designs were tested, one with a water to cement ratio 0.45 and cement content 350kg/m3, and the other with a water to cement ratio 0.80 and cement content 260kg/m3.
This raises a concern that treating a cracked surface with silane, or treating a surface that cracks after treatment, might result in a similar effect to that observed by Titarelli and Moriconi if the surface is exposed to splashing or occasional immersion. This situation was investigated by Dai et al (2010), who tested concrete with a water to cement ratio 0.68 and cement content 248 kg/m3. They found that for silane and silane-siloxane surface treatments, corrosion after one year of exposure to salt spray was closely related to penetration depth:
• Silane treatments, which penetrated at least 5mm, prevented reinforcement corrosion in uncracked
concrete specimens.
• Silane-siloxane and silicate treatments, which penetrated less than 5mm, did not reduce corrosion
in uncracked specimens.
• Silane impregnation of cracked specimens prevented corrosion provided that the silane's
penetration depth exceeded 5mm.
• Silane and silane-siloxane treatments that penetrated up to 5mm reduced corrosion when applied
to cracked specimens, but did not prevent it.
• Silane and silane-siloxane treatments applied before crack formation prevented corrosion when the
penetration depth equalled or exceeded cover depth, but was less effective when the penetration depth was less than the cover depth.
The authors concluded that when silane penetration depths equal or exceed cover depth, then the concrete around the steel is water repellent and therefore contains little or no capillary water, reducing
Performance of surface treatments
the conductivity of the concrete and thereby reducing corrosion rates and extending service life. They concluded that if cracks form after treatment, then retreatment is necessary unless the cracks are very fine, eg less than 0.08mm.
Dai et al (2010) found that silane surface treatments reduced corrosion activity in cracked concrete when the depth of penetration exceeded the depth of cover, while Titarelli and Moriconi (2008) reported that silane admixtures increased corrosion activity in cracked concrete. Dai et al exposed their test specimens to intermittent salt spray, whereas Titarelli et al's specimens were continuously immersed in a salt solution. The difference between the two sets of results probably reflects the different exposure conditions: in unsaturated concrete, silane reduced the moisture content at cathodic sites to an extent where electrical conductivity was reduced (ie moisture availability was the rate-determining step), but in concrete that would otherwise be saturated, silane reduced moisture content at cathodic sites to an extent where conductivity was still high but oxygen was more available. Therefore the effectiveness of silane/siloxane treatments on cracked concrete probably depends on the moisture content (ie exposure conditions) of the particular concrete.
The trials by Dai et al (2010) found that the silicate-based treatments were generally less effective than the silane/siloxane treatments: they did not prevent corrosion on uncracked specimens or when applied to cracked specimens, although in some circumstances they reduced corrosion when applied before cracking. The performance of these materials was not consistent and the authors did not attempt to explain it, other than to relate it to poorer resistance to water and chloride ions.
4.7 Durability of treatment
Examples of indicators of treatment durability specified by various agencies are presented in appendix A, table A5.
Any product that is selected for use must be able to withstand the alkalinity of the concrete surface. This aspect is covered by some of the acceptance criteria (see table A5).
The durability (longevity) of the treatment is largely determined by the exposure conditions and by penetration depth, which in turn is determined by concrete quality and moisture content, as well as application technique. Thus, different investigations of treatment durability will produce different results.
The in-situ monitoring reported by Darby et al (1996), and described in section 4.6, indicated that the concrete was still losing moisture seven years after treatment. These observations may be more relevant to the proposed use of surface treatments in New Zealand than observations based on the performance of treatments on bridge decks or other surfaces exposed to physical wear.
Weyers et al (1994) reported the findings of a 1989 survey of highway agencies in the US – the responses from about 30 agencies indicated that the service life for concrete sealers is considered to be about five years for deck surfaces, and about 10 years for other surfaces exposed to run-off or splash/spray. These findings have been widely cited and used in service life prediction models. The survey did not, however, distinguish between different types of sealer or define ‘service life', so it is not clear whether these estimates of service life are accurate for silane/siloxane penetrating sealers. The researchers themselves considered that the end of service life was reached when 30% of the chloride ion permeabilities measured on the sealed surface no longer exceeded that of the substrate concrete.
The influence of surface treatments on the service lives of concrete bridges
Weyers et al (1993) estimated that the service life of silanes and siloxanes applied to substructure and superstructure components is five to seven years, and recommended reapplication every six years. This was based on the surveys described above, and on observations that service life appeared to be determined by exposure to environmental agents such as ultraviolet light and moisture, rather than [on deck surfaces] by abrasion by traffic.
Laboratory and site testing by Weyers et al (1995) indicated that a service life of up to 10 years was a ‘reasonably conservative estimate' for silane/siloxanes applied to US bridge elements not subject to abrasion. This conclusion was based not simply on the durability of the treatment itself, but on modelling the rate of diffusion of chlorides through the concrete, taking into account the relative rates of chloride ion ingress through treated and untreated surfaces. The results suggested that silane/siloxane sealers applied to new concrete could maintain chloride ion concentrations less than corrosion threshold concentration at cover depth 51mm for at least 10 years, depending on the concrete quality and exposure to chloride ions. Observations, however, suggested that in practice, service life would be limited to about eight years on trafficked deck surfaces, and to about 10 years on untrafficked surfaces that were subject to natural weathering by ultraviolet light, water, wind and/or ice. In addition, service life was shown to be affected by the quality of the concrete substrate: even though substrates were grit-blasted before treatment, chloride ingress was lower through a ‘rough-trowelled' surface that had been moist-cured for seven days before treatment than through a formed surface that had been cured by leaving the concrete in the plywood form for seven days.
BD 43/03 indicates that alkyl (isobutyl) trialkoxy silane is highly effective for at least 15 years provided it is applied correctly, and that longer service lives are anticipated. It recommends assuming reapplication will be needed after 20 years.
BD 43/03 requires the need for retreatment of a structure to be determined as part of its regular inspection and assessment regime. It suggests that retreatment be considered when significant changes in half-cell potentials are observed and critical levels approached over several areas of the element.
The Department for Transport (England)
Code of practice (2005) reported that little data exists on the likely service life of silane treatments and that effective life is difficult to determine.
Raupach and Wolff (2005) found that for up to one year of exposure, the durability of treatment was related to neither penetration depth nor concentration of active ingredient, and suggested further research into the mechanism of failure of surface treatments.
Sandeford et al (2009) considered that the durability of silane treatments would vary significantly with exposure conditions. As part of the maintenance programme associated with a port facility, they have instituted a programme of testing whereby treated concrete surfaces are tested every 10 years, with a view to reapplying the treatment once the water-repellent effect observed on core samples diminishes.
Measurements of chloride ingress into samples exposed to tidal, splash and atmospheric conditions suggest that the benefits of silane treatment are less significant after seven years than at earlier ages (McCarter et al 2008), which supports the observations reported by Weyers (1993).
On the basis of a review of techniques to manage reinforcement corrosion in new and existing concrete for VicRoads, Ng (2006) recommended assuming a service life of 10 years for silane treatments. VicRoads documentation indicates that if properly applied, a silane/siloxane treatment should last 10–15 years (see section 3.1.6).
Performance of surface treatments
Ho and Ritchie (1992) estimated that the service life of ‘coatings' was probably about 5–10 years.
Few of the products currently available have been used for long enough to provide experience of their in-situ durability, and application practices have also been refined since surface treatments were first applied. More accurate information about the service life of current products will only become available with users reporting their experiences to the asset management community.
4.8 Extension of service life
The examples described in the previous sections demonstrate that the extension of bridge/element service life that surface treatments can provide clearly depends on the exposure conditions, concrete quality, cover depths and the reduction in water/chloride ingress achieved by the treatment.
It also depends on the treatment being maintained effectively. If maintenance of the treatment is overlooked or delayed, perhaps because of changes in ownership, changes in responsibility for managing the structure, changes in the owner's or manager's asset management practices, or simply funding priorities, then the benefits of the treatment will be relatively short-lived. Nevertheless, without maintenance the treatment may be sufficient to maintain serviceability for a finite period while, for example, a new structure or alternative route is planned.
Ho and Ritchie (1992) pointed out that surface treatments that allow the concrete surface to dry may reduce the time to corrosion initiation (by accelerating carbonation – see section 4.4 of this report), but that subsequent corrosion rates would be slower than in untreated concrete, thus extending the time until the corrosion damage becomes sufficiently severe or extensive to be considered unacceptable. They stressed that such an extension of the propagation phase depends on the treatment being maintained so that it retains its waterproofing properties over the exposure period, and ventured the opinion that application of coatings without an established maintenance programme could be judged as misusing the material and being a waste of resources.
Sandeford et al (2009) considered that the time to corrosion initiation on the new structure in their case study could be extended by up to 90 years if sufficient silane was applied, and if the quality of impregnation was maintained by reapplication at appropriate intervals, the intervals varying beween different exposure conditions (see section 4.7 of this report). They concluded that silane application needs to be well controlled to achieve the required quality of impregnation needed to extend service life (see section 4.5).
Ng (2006) indicated that silanes may extend service life by 4–10 years, but did not explain the basis for this.
The most comprehensive reports on service life extension are from work in the US, where laboratory and field observations have been used to develop models for predicting the extension of service life.
Weyers et al (1993) stated that with periodic applications of sealer (including silane/siloxanes), the estimated service life of patch repair, encasement and jacketting rehabilitation methods is 50 years.
The service life extension achieved by applying silane/siloxane as a preventive treatment depends on the level of chloride ion contamination in the cover concrete. Weyers et al (1994) pointed out that although surface treatments will minimise further ingress of chloride ions, chlorides already present in the concrete when the treatment is applied will redistribute by diffusion driven by concentration gradients. They described a method of using a diffusion-based model to predict the time to corrosion
The influence of surface treatments on the service lives of concrete bridges
initiation after surface treatment. This method can be used to identify whether the chloride contamination before treatment is low enough for the surface treatment to extend the service life by a significant period, or whether the chloride contamination is already too high for the treatment to offer significant benefit. They noted, however, that such modelling is impractical for routine maintenance decision making. For this purpose, they suggested a relatively simple linear model for predicting the time at which the chloride ion concentration at cover depth would reach corrosion threshold. This model is based on the observation that after treatment, the percentage decrease in chloride ion concentration near the surface is very similar, irrespective of original concentration, and on the assumption that the total amount of chloride ion in the concrete remains constant after treatment. This approach gave a slightly conservative estimate of time to corrosion initiation, but this was considered acceptable for practical purposes.
Weyers et al (1995) considered that in practice, the service life of the treated structure would be limited by the durability of the treatment (see section 4.7 in this report), but demonstrated by diffusion-based modelling that a structure that was treated when new could achieve the required service life (time to corrosion initiation) of 50 years if treatments were reapplied after each predicted ‘treatment service life'. They noted, however, that the corrosion protection periods for structures treated after contamination with chlorides are likely to be less than 50 years.
Zemajtis and Weyers (1996) used the same data to model the ‘corrosion protection time' for US bridges, taking into account the relative rates of chloride ion ingress through treated and untreated surfaces and the change in surface chloride content with time. The model indicated that silane/siloxane treatments could extend service life (time to corrosion initiation) by 40–50 years, depending on concrete quality, cover depth, exposure to chloride ions and to agents that degrade the surface treatment. The model assumed that the surface treatment was reapplied as necessary to maintain its effectiveness. They also stressed that surface treatments should not be used to justify acceptance of poor-quality concrete, because chloride ion diffusion rates (which are determined by concrete quality) significantly influence the predicted service life.
4.8.1 Predicting service life
Predictions of ‘service life' may vary depending on how service life is defined.
Time to corrosion initiation is relatively easy to predict from chloride ion concentration gradients, so most predictions of ‘service life' are based on time to corrosion initiation (‘limit state 1' as described in appendix B). This is a relatively conservative approach to managing corrosion, because the consequences of inaccuracy are less severe than defining the end of service life in terms of a particular degree of damage. Thus, time to corrosion initiation is appropriate for cases where corrosion would cause an unacceptable failure, such as for prestressed elements.
The time from corrosion initiation until sufficient corrosion product has been generated to crack the cover concrete (‘propagation time') is more difficult to predict because it is influenced by many more factors, including:
• corrosion rate – determined by availability of water and oxygen
• reinforcement bar diameter and composition
• volume of corrosion product – determined by oxidation state
Performance of surface treatments
• concrete strength, porosity and elastic modulus
• cover depth.
In addition, several limit states during the propagation phase may be used to define ‘propagation time', as indicated by limit states 2a–2e as described in appendix B.
The propagation time in untreated concrete in aggressive conditions may be much shorter than the time to corrosion initiation. For example, Weyers et al (1994) and Zemajtis and Weyers (1996) considered three to five years to be a reasonable estimate of propagation time for US bridge decks, based on observation and literature review. Sohanghpurwala (2006) quoted similar values modelled for typical US highway concretes with cover depths of about 50mm.
Published information on propagation times for New Zealand structures is limited, but information may be available on specific structures where ongoing inspections have revealed new corrosion damage after a condition survey in which chloride contents were measured. This may include structures on which surfaces were treated or coated to reduce or prevent corrosion damage.
More accurate information about the service life extension offered by surface treatments of current products will only become available if asset managers actively monitor the performance of treated (and untreated) structures and report their experiences to the asset management community.
4.9 Effects of surface treatments on other processes
After applying an initial surface treatment, a bridge owner/manager may subsequently decide to apply a different treatment. For example:
• A different type of water-resistant surface treatment may be selected if the original is no longer
available or if a more water-resistant treatment is desired.
• Architectural or antigraffiti coatings may be desired for aesthetic reasons or to manage antisocial
• A more cost-effective long-term protective treatment may be subsequently needed (eg cathodic
These possibilities should be considered before the surface treatment is applied, because the original surface treatment may reduce the bond of the subsequent treatment and will influence the operating parameters of cathodic protection systems.
When water passes through concrete and evaporates from the surface, it can leave surface deposits of soluble salt crystals known as efflorescence. If a surface treatment blocks the passage of liquid water but allows the passage of water vapour, then the soluble salts may crystallise below the concrete surface, causing it to delaminate. Pore-blocking treatments are less likely to cause this effect than hydrophobic treatments. If efflorescence is present on a concrete surface that is to be treated, then the possibility of water ingress from other surfaces should be investigated, and the risk of ongoing ingress addressed, before applying any surface treatment or coating.
Ho and Ritchie (1992) showed that the application of water-resistant ‘coatings' to new concrete prevented the ongoing curing of the concrete surface that occurs in service with exposure to rain. As a result, the concrete beneath the depth of coating penetration exhibited similar rates of water
The influence of surface treatments on the service lives of concrete bridges
absorption to concrete that received no curing or was not exposed to rain. These rates of absorption were significantly faster than for untreated concrete that had been exposed to rain, or for reference concretes that had been moist-cured for seven or 28 days. The effect was the same, irrespective of whether the coating was a barrier to carbon dioxide. This suggests that application of a surface treatment at the time of construction is not necessarily beneficial: satisfactory penetration may be difficult to achieve on a well-cured surface, so that frequent reapplication would be required for the treatment to remain effective; while on a poorly cured surface (formed or trowelled), the ultimate quality of the cover concrete beneath the surface treatment may be reduced, because water that would otherwise be available for ongoing curing can evaporate more readily.
Considering that most of the reviewed literature reported the use of surface treatments on structures exposed to de-icing salt, it is surprising that little information was found about the effect of surface treatments on freeze-thaw resistance. Perenchio (1988) reported that field studies in the US and Germany showed that silane did not affect the freeze-thaw durability of the concrete. In contrast, he found that the results from various laboratory tests were variable and often conflicting, and concluded that this was because laboratory test conditions often did not accurately represent field conditions. Therefore, the apparently short life of surface treatments reported by Weyers et al (1993 and 1994) for bridges exposed to de-icing salts probably reflects the inherent resistance of the concrete surface to freeze-thaw and physical wear, rather than the surface treatment having a deleterious effect on concrete durability.
4.10 Overall benefits of surface treatments
The independent references summarised in section 4 indicate that surface treatments based on silane/siloxane:
• may significantly reduce the ingress of moisture and chloride ions in concrete exposed to seawater
splash, spray and ponding
• reduce corrosion activity in uncracked concrete
• reduce or increase corrosion activity in cracked concrete depending on the concrete's moisture
content, the depth of impregnation, the cover depth, and whether the concrete cracked before or after treatment
• range in effectiveness depending on the concentration of active ingredient, and the depth and
uniformity of impregnation achieved, which in turn is determined by the uniformity and rate of application, concrete quality, and concrete moisture content and surface quality at the time of application
• achieve better penetration when applied as creams or gels, because the treatment does not
evaporate or drain from the surface during application
• are not permanent, needing to be reapplied at regular intervals of 10–20 years, depending on
exposure conditions and depth of impregnation
• may increase carbonation rates, but may reduce the rate of subsequent corrosion, depending on
the concrete's moisture content
Performance of surface treatments
• may, if correctly maintained, significantly extend the service life of a structure, depending on
quality of application, exposure conditions, level of chloride ion contamination at the time of treatment, and cover depths
• may be less beneficial to high-quality concrete or well-cured new concrete, because it can't
penetrate as deeply
• may reduce the ultimate quality of concrete when applied to poor-quality or poorly cured new
concrete, by preventing the ingress of water that would otherwise assist ongoing curing.
These sources also suggest that silicate-based pore-blocking surface treatments:
• are less effective than silane/siloxane treatments in reducing the ingress of moisture and chloride
• are generally less effective than silane/siloxane in reducing corrosion activity
• may be more effective than silane/siloxane treatments in reducing carbonation, but not as effective
as acrylic membranes – as carbonation-induced corrosion is not common on New Zealand bridges, this type of product may be less suitable for managing reinforcement corrosion on New Zealand bridges.
Nevertheless, if the trade literature demonstrates that a specific silicate-based product meets appropriate requirements of one or more road-controlling authorities and therefore is an effective barrier to ingress of chloride ions and moisture, then the product may be considered.
Cement-based pore-blocking treatments are used for waterproofing, so may be more effective than silane/siloxanes where exposed to water under pressure, eg on elements that are immersed or exposed to groundwater. No evidence of this was reported in the sources reviewed.
The influence of surface treatments on the service lives of concrete bridges
When and how to apply surface treatments
The decision to treat a bridge will be determined by consideration of the treatment's cost and potential benefits.
Routine maintenance throughout a bridge's life provides cost savings over the life of a structure by slowing gradual deterioration processes and extending the service life of the bridge (Smith and Simpson-Bint 2009). If such maintenance is delayed, then more significant maintenance costs will be incurred later on. Appendix C describes how regular small levels of intervention contribute to maintaining desired levels of service without excessive expenditure.
Preventive surface treatments may be seen as an extension of such maintenance cycles. If applied when the need is identified and at the optimum time, they may be seen as ‘routine maintenance' that falls within the description given in appendix C. If applied before the optimum time, then the cost may outweigh the future economic benefit.
Life cycle costing is used to identify the economic impact of maintenance and other interventions, and thereby to assist with prioritising different intervention options.
The
Economic Evaluation Manual (NZTA 2010) describes the NZ Transport Agency's method for evaluating life cycle costs, whereby net present values are calculated from estimates of initial and ongoing costs over the period of interest. Net present values enable the comparison of the costs of different maintenance options applied at different times.
The life cycle cost is heavily influenced by the discount rate (rate of return) used. At current discount rates, this approach requires costs to be assessed for periods up to 30 years; beyond 30 years, the effect of discounting significantly reduces the benefits of future cost savings A service life extension of up to 30 years may be a realistic expectation for a bridge when preventive treatment is being considered, depending on the needs of the particular structure.
Although the direct costs associated with applying a preventive surface treatment may be less than the direct costs of repairing elements that need repair in the future (see appendix B), the net present value of the preventive treatment may be higher. In addition, the life cycle costs of applying repeat cycles of a surface treatment to prevent corrosion damage will probably be greater than the life cycle costs of repairing damage caused by reinforcement corrosion. The NZ Transport Agency's current discount rate, 8%, is relatively high and would make it difficult to justify surface treatments on an economic basis alone. A lower rate, such as the 3.5% rate currently used by the Highways Agency, may provide a more realistic whole-of-life solution, and thereby encourage the use of preventive maintenance such as surface treatments.
It is difficult to quantify the potential benefits of a preventive surface treatment on a particular bridge without extensive (and costly) investigation, so it may be difficult to demonstrate at the planning stage that it can reduce life cycle costs. Nevertheless, it may be possible to justify a preventive surface treatment by accounting for as many risks and factors as possible in the economic evaluation, and
4 In England, the discount rate for economic evaluation of maintenance works was reduced from 8% to 7%, then to 3.5%, because investment decisions were being unduly postponed. Reducing the discount rate to 3.5% meant that the evaluation period was effectively extended to 60 years.
Applying surface treatments
presenting supporting evidence to qualitatively describe the benefits. The following sections describe the risks and factors that need to be taken into account.
It was inappropriate for us to estimate quantitative benefits, such as an optimum ‘time before corrosion damage appears' at which applying a preventive surface treatment becomes cost effective, because too many site-specific variables are involved. Instead, we have used the findings reported in sections 3 and 4 to identify the situations in which a bridge might technically benefit from preventive surface treatment, so that bridge asset managers can evaluate the risks and estimate costs associated with treating individual structures that meet these criteria.
5.1 The optimum time for intervention
Appendix B describes how corrosion damage develops with time.
Appendix C describes how different types of intervention (routine maintenance, renewal and upgrading) affect the overall performance of the structure.
Preventive maintenance, such as applying a surface treatment, aims to delay corrosion initiation and reduce the subsequent rate of corrosion, thereby minimising corrosion damage at a given time during the service life of the structure. Preventive maintenance is undertaken before the first damage occurs, ie in the initiation phase or early in the propagation phase (before limit state 2a, as described in appendix B). Preventive treatments usually require ongoing maintenance to ensure that they remain effective, with the possible exception of pore-blocking impregnations (see section 4 regarding the effectiveness of such materials).
Repair/rehabilitation is undertaken after damage becomes evident, and may need to be repeated regularly to ensure that the performance of the structure remains acceptable.
The rate of deterioration accelerates with time, as do the cost of the associated repairs and the risks associated with the severity of damage.
Similarly, the optimum time for intervention is determined by the risks associated with each level of damage and the life cycle costs associated with the method of intervention. For example, applying a silane/siloxane treatment early in the initiation phase will significantly extend the time to corrosion initiation and has relatively low up-front costs, but will require ongoing applications during the service life of the structure. Therefore the life cycle costs of this approach are likely to be high, particularly if access costs for each application are high.
The number of repeat preventive treatments or subsequent repairs within the required service life can be reduced by intervening in the deterioration process as late as possible. The ideal would be to apply a silane/siloxane treatment late in the initiation phase, because the propagation phase can be relatively short in aggressive environments (see section 4.8). But even if significant chloride ingress is not identified until early in the propagation phase, surface treatment may still be beneficial if applied before the rate of corrosion and the likelihood of damage become significant (limit state 2a as described in appendix B). The risks associated with individual bridges will determine how long treatment may be delayed. For example, treatment may be delayed longer on reinforced structures than on prestressed structures, because the consequences of conventional reinforcing bar corroding are less significant than the consequences of prestressing steel corroding (see section 5.3).
The influence of surface treatments on the service lives of concrete bridges
5.2 New structures
In principle, surface treatments are most effective in preventing or delaying reinforcement corrosion when applied to new structures, ie before they have been exposed to seawater, seaspray or saline runoff. Thus BD 43/03 requires that new structures are treated as soon as possible after an initial seven-day curing period. The most convenient time to apply the treatment is during construction, particularly for precast elements. Thus Ng (2006) recommends silane treatment for new precast components in many coastal or inland saline exposure conditions, but not for existing structures.
In practice, applying surface treatment at the time of construction may have adverse effects on both the effectiveness of the treatment and/or the ultimate quality of the cover concrete beneath the treated layer (Ho and Ritchie 1992; also see section 4.9 of this report). In addition, the treatment will need on-going maintenance throughout the structure's service life to ensure that it remains effective. This requires commitment from its owner in the form of an effective asset management programme and appropriate maintenance budgets.
In addition, the New Zealand standard specifications for concrete design (NZS 3101), concrete supply (NZS 3104) and concrete construction (NZS 3109) have, since 1995, specified concrete materials and methodologies that, if followed, should deliver structures that are inherently more durable than those currently reaching the end of their design life. For example, the use of supplementary cementitious materials (such as fly ash) in concrete exposed to seawater or spray has been shown to reduce the incidence of corrosion in bridge populations (Chirgwin et al 2009). Therefore, concrete bridges built to recent/current standards may not benefit from early application of surface treatments as much as earlier structures might have done.
As has been noted by other road-controlling authorities (see section 3), close attention to durability design and construction quality should be considered the key to achieving the required durability. Good site supervision is essential to ensure that the depth and quality of concrete cover comply with the project specification. To minimise the risk of premature corrosion on at-risk structures (ie coastal and prestressed bridges), it may be appropriate to increase cover depths beyond the minimum required by NZS 3101.
Surface treatment at the time of construction may, however, be appropriate where the quality of materials or construction does not meet the aforementioned standard specifications. In such cases, silane/siloxane surface treatments alone should not be used to remedy the defect, because the durability of the concrete will rely on regular maintenance of the treatment, which in practice is likely to be delayed, overlooked or neglected. Instead, they may be used to supplement patch repair or other remedial treatments.
Indeed, NZS 3101:2006 allows the use of ‘protective surface coatings' to extend the life of new structures, but cautions that ‘an inadequate, poorly maintained coating may lead to more rapid degradation than no coating'.
Therefore although less convenient, it will generally be more cost effective to manage the corrosion risk in a bridge population by applying a surface treatment after a bridge has been in service for a while, as described in section 5.3, rather than by treating every bridge in a particular exposure environment at the time of construction.
Applying surface treatments
5.3 Existing structures
Decisions to rehabilitate bridges are generally based on (in order of frequency):
• the amount of deterioration
• the availability of labour and funding
• the condition of other parts of the bridge
• the volume of traffic
• the rate of deterioration (Weyers et al 1994).
These factors also apply when deciding how to prioritise preventive surface treatment on a particular bridge. Other factors that will influence the decision are:
• the required remaining service life
• whether regular repeat treatments can be applied
• whether reducing the moisture content of the concrete and ingress of additional chlorides will be
sufficient to significantly increase service life.
Silane/siloxane treatments may be applied as part of a repair system. The treatment may be extended, as a preventive measure, to elements that do not currently need repair. This situation is not discussed here because it would generally be practical and economic to apply a preventive treatment in these circumstances.
Surface treatment with silane/siloxane alone may not be appropriate for deeply carbonated concrete (see section 4.4). The use of surface treatments to manage carbonation-induced corrosion is not considered here because carbonation rarely causes severe corrosion damage on New Zealand bridges.
BD 43/03 requires the decision to treat an existing structure to be based on its condition as evidenced by a visual ‘fingertip' survey, or by assessment of the risk indicated by measurement of half-cell corrosion potentials and chloride ion contents. Using gradients of corrosion potential to identify ‘hot spots' of elevated corrosion risk may, however, be more useful than the BD 43/03 approach of using the magnitude of corrosion potential. This is because very negative potentials may result from conditions that in fact reduce the corrosion risk and therefore do not necessarily indicate active corrosion (ie repair may be needed rather than preventive treatment) as implied by BD 43/03.
Weyers et al (1993) indicated that surface treatments are not appropriate if the steel has already started to corrode, or if the chloride ion concentration at the reinforcement has reached corrosion threshold levels (approximately 0.59kg/m3 of concrete) or will do so within the required remaining life of the structure. They also described a statistical modelling approach to assessing the time to corrosion initiation. The linear model for predicting time to corrosion initiation after sealing (Weyers et al 1994) provides a more practical approach.
Sohanghpurwhala (2006) developed the sampling and modelling concept further by introducing a ‘susceptibility index' calculated from chloride ion concentration profiles collected from several locations on the structure. He indicated that surface treatments may provide sufficient extension of service life for elements with relatively low chloride concentrations at cover depth, but where ‘do
The influence of surface treatments on the service lives of concrete bridges
nothing' is no longer appropriate. At higher levels of chloride contamination, he indicated that more extensive remedial work would be needed.
Decisions based on increasing the time to corrosion initiation may be overly conservative, because an
effective surface treatment will reduce the moisture content of the concrete, and thereby reduce the
corrosion rate (Ho and Ritchie 1992). Therefore it may also be appropriate to treat an element that is
already critically contaminated but which shows no sign of active corrosion, particularly if a finite
service life is required. For example, within the next 10–20 years, the element could be due for
replacement to increase load capacity, or the road might need to be realigned, making the bridge
redundant. Regular monitoring of the condition of the element would be required in such
circumstances. BD 43/03 follows this approach by requiring ongoing monitoring of half-cell corrosion
potentials on treated structures where chloride ion concentrations exceed 0.3% by weight of cement (about 0.95kg/m3, or 0.04% by weight of concrete) at the level of the reinforcement.
The accuracy of evaluations based on statistical models such as those mentioned above, or on models that predict the time to corrosion damage (‘propagation models'), relies on the accuracy of the input data – in particular, the actual range of cover depths and chloride ion profiles. Propagation modelling, statistical modelling, and carrying out a sensitivity analysis on the range of input data, are relatively complex tasks. Therefore they are more appropriate for managing the corrosion risk on a relatively major structure, particularly when the assessment is reactive, ie in response to corrosion being observed during inspections carried out in accordance with the NZ Transport Agency's bridge inspection policy (NZ Transport Agency 2009).
Asset managers need a different evaluation process when they are considering preventive treatments for populations of bridges that may be at risk, ie when they are taking a proactive approach. To address this need, the following sections suggest a simpler, subjective process for identifying bridges that may benefit most from surface treatments. Section 5.3.1 describes bridge populations that are most likely to benefit, and section 5.3.2 describes how to identify individual bridges within those populations that merit closer assessment.
The process of selecting bridges for preventive treatment is in some ways akin to the current programmes for assessing and addressing risks associated with seismic performance and scour, and could be managed in the same way.
5.3.1 Identifying bridge populations that would benefit from surface
The first step in the process is to identify populations of bridges in which individual structures might benefit from surface treatments.
The principles used to identify such populations are as follows:
1
Design standards – Elements built in accordance with NZS 3101:1995 or subsequent revisions
should deliver a service life of 50 years without surface treatment, and bridge elements built in accordance with NZS 3101:2006 or subsequent revisions should deliver a service life of 100 years without surface treatment.
2
Age – Elements built in accordance with NZS 3101:1995 or subsequent revisions should not show
significant ingress of water or chloride ions within 20 years of construction.
Applying surface treatments
3
Exposure conditions – The risk of chloride-induced corrosion is greatest in concrete exposed to
air and seawater and/or seaspray. Thus the risk is relatively low in bridges/elements in NZS 3101 exposure classifications A2 (inland), B1 (coastal perimeter) and B2 (permanently submerged). The risk is higher in bridges/elements in exposure classifications B2 (coastal frontage) and C (tidal/splash/spray), and is particularly sensitive to microclimates within these zones that may locally increase exposure to seawater, seaspray or run-off.
4
Construction defects – Corrosion is unusual on well-constructed bridge elements within 20 years
of construction, or on bridges in the NZS 3101 exposure classifications A2 and B1. Therefore such cases may be the first evidence of widespread construction-related shortcomings that will also cause premature corrosion on other elements. For example, particular designs, construction methods or construction defects may result in insufficient cover in one or more elements; concrete cast in the 1960s and 1970s may have contained chloride-based admixtures. Corrosion on relatively new structures, and on structures in exposure classifications A2 and B1, should be investigated to identify the cause of corrosion, so that preventive treatments can be considered for other elements likely to be affected in the future.
5
First evidence of imminent widespread corrosion – Localised corrosion damage affecting only a
few bridge elements, or parts of elements, may be the first evidence of widespread ingress of moisture, chloride ions, and/or the possible presence of chlorides added to the concrete at the time of construction. Thus they may indicate imminent corrosion on other elements. Such cases should be investigated to identify the cause of corrosion so that preventive treatments can be considered for other elements likely to be affected.
6
Limitations of ‘best practice' – NZS 3101 solutions were based on the best available knowledge at
the time. Long-term performance may reveal limitations that were not recognised when the NZS 3101 durability clauses were introduced and subsequently revised. Ongoing monitoring of chloride ion ingress and half-cell corrosion potentials on bridges built to this standard specification may identify such limitations and enable preventive treatment before corrosion causes visible damage. It may also provide feedback for future updates to NZS 3101.
7
Preventive vs remedial treatment – Silane/siloxane treatments may extend the time to corrosion
initiation and reduce the subsequent rate of corrosion, but they will not restore the performance of elements damaged by corroding reinforcement.
8
Benefits and limitations of treatment – Silane/siloxane treatments cannot protect against ingress
of water under pressure. Silicate treatments may improve water resistance in such environments but other approaches, such as jacketing, may be more effective.
9
Defects identified during construction – Silane/siloxane treatments may be applied during
construction as part of remedial work or as preventive treatment to reduce the risk of corrosion associated with shortcomings in materials or workmanship.
10
Non-structural steel corrosion – Where corrosion damage does not affect structural performance,
and deterioration is likely to remain localised (eg as in the examples in principle 4 above), then silane/siloxane treatments may prevent further damage to steel or cover concrete.
The influence of surface treatments on the service lives of concrete bridges
Table 5.1 describes categories of bridges or bridge elements unlikely to benefit from surface treatments. Preventive treatments do not need to be considered when planning asset management programmes for these bridges/elements.
Table 5.1
Types of structure/element unlikely to benefit from preventive surface treatments
Category
Principle
Exception
Principle
To remedy defects during construction
Less than 20 years old
Where one or more elements show
signs of localised corrosion
In NZS 3101 exposure classification A2
Where one or more elements show
signs of localised corrosion
Elements exhibiting corrosion damage
If corrosion damage is purely aesthetic
and if cover concrete is unlikely to spall
Elements that are permanently or
regularly immersed (NZS 3101 exposure classification B2 (immersed))
Table 5.2 describes categories of bridges or bridge elements that may benefit from surface treatments. Preventive surface treatments should be considered in asset management programmes for these bridges/elements.
Table 5.2
Types of structure/element that may benefit from preventive surface treatments
Bridge/element type
Principle
Exception
Principle
New, to remedy construction defect
Any age, any NZS 3101 exposure
Elements on which structural steel is
classification, where one or more
elements show signs of localised corrosion
More than 20 years old, in NZS 3101
Elements on which structural steel is
exposure classification B2 (coastal
Within the categories identified in table 5.2, the need for evaluation and treatment should be further prioritised to account for specific features of microclimate, and/or element design that will affect the risk of corrosion, such as the following examples:
Type of reinforcement – Corrosion of prestressing steel presents a greater risk than corrosion of
reinforcing bar.
Specific design features – Bruce et al (2008) identified that the corrosion risk associated with
pretensioned concrete beams on bridges built in the 1950s, 1960s and early 1970s is higher than
in bridges built after the mid-1970s, because the prestressing strand in the earlier beam designs is
not fully confined by stirrups, and specified cover depths were relatively low (less than 30mm). In
more recent designs, the strand is confined by stirrups; the stirrups would corrode first, providing
a relatively low-risk warning of future structural damage.
Microclimate – Bruce et al also identified that bridges close to open surf beaches are at greater
risk than other bridges in the NZS 3101 exposure classification B2.
Applying surface treatments
Thus the highest priority should be to evaluate the risks on prestressed beams on bridges built before the mid-1970s that are within 200m of an open surf beach. Evaluation of bridges of the same design in more sheltered environments, and younger bridges within 200m of an open surf beach, may be considered a lower priority.
Similarly, reinforced concrete bridges close to an open surf beach may be considered a high priority for evaluation if corrosion is evident on some elements, but not as high a priority as prestressed concrete in the same environment.
5.3.2 Identifying individual bridges that may benefit from surface
The second step is to identify individual bridges within those groups on which application of a surface treatment may extend the time to repair and/or reduce the extent of repair needed in future.
This involves evaluating the corrosion risk on individual bridges by on-site measurements of cover depth, half-cell corrosion potential and chloride ion contamination. The results from these measurements are then used to predict the time to corrosion initiation. Once this is known, the benefits of surface treatment can be assessed, and the time of application determined to optimise life cycle costs.
In addition to principles 1–10 presented in section 5.3.1, principles 11–13 also apply:
11
Convenience – Bridges/elements that may benefit from a surface treatment should be investigated
at least once every 20 years after construction to evaluate the need for surface treatment. For convenience, the on-site investigation could be carried out as a Special Inspection at the same time as the six-yearly Detailed Inspection, or shortly thereafter, especially where special access facilities are needed. This would enable the findings to be considered at the same time as observations from the Detailed Inspection. For bridges built since 1996, the first such inspection should be at 18 years after construction. The findings of each evaluation would determine the frequency of subsequent investigations. For example (but note that the actual monitoring frequency would be determined case-by-case):
If immediate intervention is deemed to be beneficial (eg corrosion initiation is imminent or has
been reached but no corrosion damage has yet occurred), the bridge would be treated before the next Detailed Inspection.
Monitoring intervals of six years (every Detailed Inspection) are recommended where the initial
(or previous) evaluation indicates corrosion initiation is imminent but the risk does not warrant immediate treatment.
Monitoring intervals of 12 years (every second Detailed Inspection) should enable timely
intervention where the initial (or previous) evaluation indicates corrosion initiation is likely before the bridge becomes functionally obsolete, but the risk does not warrant immediate treatment.
Monitoring intervals of 18 years (every third Detailed Inspection) should be sufficient where the
initial (or previous) evaluation detects insignificant chloride ion ingress within 10–25mm of the reinforcement, depending on concrete cover depth.
The influence of surface treatments on the service lives of concrete bridges
Thus the timing of evaluation and ongoing monitoring should be based on the programme for six-yearly Detailed Inspections. It is recommended thst the NZ Transport Agency's regional asset management plans and bridge inspection policy are amended to include appropriate investigations/monitoring as Special Inspections.
12
Time to corrosion initiation – Applying a surface treatment before the concentration of chloride
ions at the reinforcing steel has reached corrosion threshold concentrations increases the likelihood that the treatment will delay the onset of corrosion and significantly delay the development of significant corrosion damage. This is the preferred approach.
13
Time to corrosion damage – Applying a surface treatment after corrosion initiation, but before
sufficient corrosion product has been generated to crack the cover concrete, should slow the corrosion rate and thereby delay the development of corrosion damage. This approach may be necessary if the first evaluation is carried out after corrosion initiation. Treatment of reinforced concrete may be delayed until close to, or slightly after, corrosion initiation, provided that the risk associated with a small amount of corrosion is acceptable. Purposely delaying treatment of prestressed concrete until close to or after corrosion initiation is not recommended, however, because even a small amount of corrosion can significantly reduce structural performance.
Significant corrosion sometimes occurs without visible damage to the surface concrete. Site investigation is needed to detect such cases. Principles 14–17 describe the situations in which this may happen.
14
Localised corrosion – Chloride-induced corrosion can significantly reduce the cross section of
reinforcing steel in very localised areas known as ‘pits'. The relatively small volumes of corrosion product formed in the pit may not generate sufficient pressure to crack the cover concrete, so the cross section of the bar can be significantly reduced at pits before the corrosion is detected. Measurement of half-cell corrosion potentials may help to identify localised areas on a concrete element where corrosion is more likely. Exposing the reinforcing steel at these ‘hotspots' will reveal whether it is corroding. Actively corroding areas should be repaired before applying a surface treatment. If the steel at the hotspots is not corroding, then surface treatment may delay the onset of corrosion.
15
Corrosion in anaerobic environments – Where oxygen availability is limited, eg in concrete in
tidal zones or splash zones where the concrete is usually saturated, reinforcing steel may be corroding, but the corrosion products may not be sufficiently oxidised to generate enough pressure to crack the cover concrete. When evaluating the corrosion risk on such elements, the reinforcement should be exposed in representative areas to ascertain its condition, irrespective of the magnitude of corrosion potential measured. Applying a breathable surface treatment to saturated concrete may enable it to dry sufficiently to increase oxygen availability at the steel, thereby increasing the corrosion rate. In addition, the corrosion products that form after treatment may be more oxidised and therefore more voluminous, generating greater expansive stress and increasing the risk of the cover concrete cracking and spalling.
16
Corrosion in porous concrete – Corrosion products may be accommodated in voids caused by
poor consolidation of the concrete at the time of construction. When this happens, they will not crack or spall the cover concrete and there may be no evidence that the steel is corroding until significant cross section has been lost.
Applying surface treatments
17
Corrosion of prestressing steel – Because of its small cross section, prestressing strand or wire
may be significantly weakened by corrosion without having produced enough corrosion product to crack the cover concrete. Thus the concrete may not crack and rust staining may not appear until the wire breaks. Depending on its composition and method of manufacture, prestressing steel may be susceptible to stress corrosion, hydrogen embrittlement, fretting and fatigue (all of which can accelerate the damage caused by corrosion alone), and half-cell corrosion potential measurements alone may not be sufficient to assess the corrosion risk associated with prestressing steel (Bruce et al 2008). Therefore, if the first evaluation of a prestressed element reveals that chloride contamination at the prestressing exceeds corrosion threshold concentrations and the cover concrete is still undamaged, then a surface treatment may be applied as a precautionary measure to slow the corrosion rate. The treated element then needs to be inspected as frequently as an untreated element approaching corrosion initiation, so that any damage is detected as soon as possible.
Tables 5.3 and 5.4 show how the 17 principles and the outcome of the site investigation may be used to determine whether or not a surface treatment may benefit a particular structure by extending the time until repair is necessary and/or reducing the extent of repair needed in future.
Table 5.3
Situations in which a surface treatment may not be appropriate
Combination of factors
Principle
Exception
Principle
Chloride contents indicate corrosion
Corrosion potentials or observations
initiation unlikely within the next 15
reveal local areas of increased corrosion
risk (eg on some beams but not others) but corrosion damage is not yet evident
Chloride contents indicate corrosion
If the effects of corrosion are purely
initiation has been reached and
aesthetic and if cover concrete is
corrosion damage is evident
unlikely to spall
(a) If corrosion initiation is unlikely within the next 15 years, then the investigation should be repeated as
described in principle 11.
Table 5.4
Situations in which a surface treatment may be appropriate
Combination of factors
Principle
Principle
Chloride contents indicate corrosion
initiation likely within the next 15 years
Chloride contents indicate corrosion
4, 5, 11–13 Patch repair damaged areas before
initiation unlikely within the next 15
applying surface treatment
years, but corrosion potentials or observations reveal local areas of increased corrosion risk
Chloride contents indicate corrosion
Regular ongoing inspections for
initiation has been reached but
corrosion damage essential for
corrosion damage is not evident
prestressed elements, even if treated
Specialists are needed to undertake the in-situ testing involved and to evaluate the results, including estimating the time to corrosion initiation and the potential extension to service life that a surface treatment may offer by reducing the ingress of moisture and chloride ions. The details of the specialist testing and evaluation are beyond the scope of this report.
The influence of surface treatments on the service lives of concrete bridges
For structures that are thus identified as potentially benefitting from surface treatment, the asset manager must evaluate the life cycle costs of surface treatment in accordance with the NZ Transport Agency methodology (NZ Transport Agency 2010).
The NZ Transport Agency's current discount rate for maintenance works is likely to favour patch repair rather than preventive surface treatments, and little quantitative information is available on the benefits of surface treatments to support an accurate economic evaluation. Therefore the economic evaluation must be accompanied by qualitative descriptions of the benefits. The relative significance given to the economic evaluation and the supporting information depends to some extent on the value of the proposed work. As noted in section 3, the cost of an accurate evaluation may be more expensive than the treatment itself.
Other factors that the asset manager needs to consider to determine whether an individual structure should be treated include:
• the remaining service life requirements
• whether maintaining the treatment at the required intervals will be practical
• the risk and indirect costs associated with future reduced levels of service that may result from
corrosion of elements on which the treatment is not maintained
• whether architectural coatings or alternative surface treatments may subsequently be used on the
• the risks and costs associated with not applying a surface treatment.
Statistical modelling to determine the life cycle benefits of treatment may be appropriate for some structures, eg very large structures, and where access costs are significant. Such modelling would involve predicting the time to corrosion initiation, with and without treatment, based on the actual range of cover depths measured, chloride ion profiles, and the level of risk considered acceptable. This approach involves extensive in-situ and laboratory testing as well as the modelling itself, and may cost several tens of thousands of dollars. It is unlikely to be practical or cost effective for most New Zealand bridges.
For most structures, a more subjective evaluation, based on the condition of the structure/elements, chloride ion profiles and service life requirements, will provide a cost-effective means of evaluation. For the purpose of this type of evaluation, it would be reasonable to assume that the interval between treatments is a maximum of 20 years and the service life can be extended by up to 20 years following each successive treatment.
For some structures/elements that may benefit from surface treatment, it may be appropriate to apply the treatment without extensive analysis because the benefit:cost ratio is likely to be favourable; for example:
• critical structures
• where the remaining service life is similar to the expected life of the treatment
• where access to the concrete surface is needed to carry out other maintenance work
Applying surface treatments
• when outer beams of a span need treatment – it may be possible to treat the inner beams at the
same time for relatively little extra cost.
If the treatment is to be applied as a ‘trial', then the possible outcomes of the trial should be considered before proceeding. For example, will the treatment prevent subsequent repairs or surface treatments bonding to the substrate, and how will it affect the efficiency of cathodic protection should it be needed? A trial application, followed by regular monitoring of chloride ion profiles and half-cell corrosion potentials on treated and untreated elements, will help to identify the benefits of the treatment in time for it to be extended to other parts of the structure if appropriate. It will, however, require the asset manager to initiate and resource the monitoring. On the other hand, a ‘wait-and-see' approach that results in untreated elements needing repair sooner than treated ones has little benefit for the structure overall, and the findings may not be directly applicable to other structures where the concrete quality, condition, exposure and/or level of chloride ion contamination differ.
5.3.3 Specifying surface treatments for New Zealand bridges
Section 4.1 describes factors that need to be considered when specifying or selecting surface treatments, but it is beyond the scope of this research to provide model specifications for surface treatments.
Specialist consultants will be able to provide appropriate specifications for materials and applications. Suppliers of proprietary surface treatments may provide specifications for application of their products, and may require that a licensed applicator apply the treatment.
Alternatively, specifications may be based on APAS (2009) or other existing Australian standard specifications. The testing associated with these specifications should be able to be procured in Australia, if not in New Zealand. Specifications based on European or US standards may be used if the associated testing can be procured readily.
5.3.4 Maintenance after surface treatment
Overseas experience suggests that silane/siloxane treatments must be reapplied at least once every 20 years to remain effective. The durability of the treatment on a particular element will vary with the product used, the nature of the substrate, the depth of penetration and the exposure conditions.
The need for retreatment is indicated by a reduction in the water repellancy of the treated surface. Therefore, after a surface treatment has been applied (including pore blocking treatments), the water repellancy of each treated surface should be checked during each Detailed Inspection by spraying water onto it. If the water is absorbed into the surface, then retreatment may be necessary.
If the treatment was applied before corrosion initiation, then chloride ion concentration profiles at a minimum of one location on the element should be measured at each Detailed Inspection after treatment, to identify whether ongoing diffusion of chlorides into the concrete has significantly increased the chloride ion concentration at the depth of the reinforcement. Once the chloride concentration at the reinforcement depth reaches the corrosion threshold, then corrosion potentials on the element should be measured to ascertain the risk of corrosion. Corrosion potentials will indicate areas of locally elevated chloride ion or moisture contents, although they will not indicate whether the reinforcement is actually corroding.
The influence of surface treatments on the service lives of concrete bridges
Similarly, if the treatment was applied after corrosion initiation, then subsequent Detailed Inspections should include a survey of corrosion potentials to ascertain whether the treatment has reduced water ingress sufficiently to minimise the risk of corrosion.
Corrosion potentials vary with ambient conditions, and chloride ion profiles may vary across an element. Therefore these properties may need to be measured several times after treatment to detect significant trends.
If the treatment was applied as a ‘trial' to part of a structure to find out whether it is worth applying to other elements, then corrosion potentials and changes in chloride ion profiles should be measured at least every six years on treated and untreated elements, to ensure that the opportunity can be taken to treat the other elements before corrosion damage occurs.
Summary and conclusions
Summary and conclusions
This section summarises the performance of surface treatments as reported by the sources reviewed, and assesses their potential for use to extend the service life of reinforced and prestressed concrete bridges in New Zealand.
6.1 Types of treatment
Surface treatments for protecting concrete reinforcement from corrosion need to reduce the ingress of moisture, chloride ions and/or air. Treatments that penetrate the concrete surface and reduce the ingress of moisture by lining or blocking pores are less susceptible to physical damage and weathering than treatments that form a continuous water-resistant barrier on the surface. They also allow the concrete to dry.
Penetrating surface treatments with potential for reducing chloride-induced corrosion include hydrophobic pore-lining treatments based on silane and/or siloxane, and pore-blocking treatments based on cementitious materials or alkali silicates.
Silane/siloxane treatments protect against moisture ingress from condensation, rain, run-off, or ponding, but are not suitable for surfaces exposed to water applied under pressure, where pore-blocking treatments may be more effective.
6.2 Experience of road-controlling authorities overseas
Many road-controlling agencies permit existing concrete bridges to be treated with silane/siloxanes if the structures are at risk from chloride-induced corrosion from exposure to splash, spray, ponding, or run-off from seawater or water containing de-icing salt. Some allow or require their use on new structures, but most prefer to address durability issues by managing the quality of concrete materials and construction.
The effectiveness of silane/siloxane treatments in reducing the ingress of moisture and chlorides and reducing corrosion activity depends on the composition of the product, the pore structure of the concrete, the moisture content of the concrete at the time of application, and the rate of application. Therefore most road-controlling agencies that permit their use specify requirements for the composition and performance of the products as supplied, application methods, and the performance of the treated surface.
Barriers to the widespread uptake of silane/siloxane treatments include:
• justifying the cost of a preventive treatment
• environmental and health/safety concerns (potentially addressed by the recent introduction of
products supplied as creams or emulsions)
• the practical difficulties associated with ensuring the substrate is sufficiently dry when the
treatment is applied
The influence of surface treatments on the service lives of concrete bridges
• difficulties associated with managing the quality and consistency of the products and of their
Pore-blocking penetrating treatments are less widely accepted than silane-siloxanes, possibly because of difficulties in demonstrating that their performance will be satisfactory and in specifying appropriate acceptance criteria.
A risk- or value-based approach is generally preferred for determining the need to treat a structure. Detailed analyses of life cycle costs may be disproportionately expensive and time consuming, compared with the cost of the treatment.
6.3 Performance characteristics
6.3.1 Silane/siloxane hydrophobic treatments
• Surface treatments based on silane/siloxane may significantly reduce the ingress of moisture and
chloride ions in concrete exposed to seawater splash, seaspray and ponding. The reduction in chloride ion contamination, compared with untreated concrete, may thus delay the onset of reinforcement corrosion, and the lower moisture content of the concrete may reduce subsequent corrosion rates.
• The effectiveness of the treatments varies, depending on the concentration of active ingredient,
and the depth and uniformity of impregnation achieved, which in turn is determined by the uniformity and rate of application, concrete quality, and concrete moisture content and surface quality at the time of application.
• Products applied as creams or gels may penetrate deeper and more uniformly because the
treatment does not evaporate or drain from the surface during application.
• The treatments need to be reapplied at regular intervals of 10–20 years, depending on exposure
conditions and depth of impregnation achieved. If correctly maintained, they may extend the service life of a structure for much longer than this, depending on quality of application, exposure conditions, level of chloride ion contamination at the time of treatment, and the depth of cover concrete.
• Silane/siloxane treatments may increase carbonation rates by allowing the concrete to dry, but the
rate of subsequent carbonation-induced corrosion is likely to be reduced. If the cover concrete contains chloride ions, the chlorides that would otherwise be chemically bound by the hardened cement paste are released by carbonation. Thus the treatments may also indirectly reduce the time to initiation of chloride-induced corrosion.
• Silane/siloxane treatments are likely to be less effective on high-quality concrete or well-cured new
concrete because they can't penetrate as deeply. In addition, the treatments may reduce the ultimate quality of poor-quality or poorly cured new concrete by preventing the ingress of water that would otherwise assist ongoing curing. Therefore they are not recommended for new bridges except as part of remedial work to address shortcomings in materials or construction.
Summary and conclusions
6.3.2 Pore-blocking treatments
Silicate-based pore-blocking surface treatments are less effective than silane/siloxane treatments in reducing the ingress of moisture and chloride ions, and are generally less effective than silane/ siloxane in reducing corrosion activity.
They may, however, be more effective than silane/siloxane treatments in reducing carbonation, but not as effective as acrylic membranes.
They may also be more effective than silane/siloxanes where exposed to water under pressure (eg on elements that are immersed or exposed to groundwater), although no evidence of this was reported in the sources reviewed.
In the future, further information on specific products may become available that indicates performance similar to silane/siloxane treatments.
6.4 Use for mitigating corrosion on New Zealand bridges
Silicate-based products may be useful for managing carbonation-induced corrosion, or chloride-induced corrosion, on immersed or buried elements. These types of corrosion are, however, relatively uncommon compared to corrosion induced by contamination of concrete by chloride ions.
Silane/siloxane treatments have the potential to extend the service life of reinforced and prestressed concrete bridges if applied before corrosion damage occurs. Because they need to be applied regularly throughout the life of the structure, they will be most cost effective if applied when corrosion is imminent but no damage has yet occurred. They may, however, offer some benefit in reducing corrosion rates of non-structural steel (ie where damage is purely cosmetic).
Close attention to durability design and construction quality is the key to achieving the required durability on new structures. Current standards for the design and construction of concrete structures should deliver a 100-year service life without surface treatments. Good site supervision is essential to ensure that the depth and quality of concrete cover comply with the project specification.
Silane/siloxane treatments should not be applied to newly built structures because they may not be able to penetrate the surface sufficiently, may result in the concrete drying prematurely and therefore not achieving its potential ultimate performance, and will need to be reapplied at frequent intervals, adding extra maintenance costs. The exception to this is when they are applied as part of remedial works, should the quality of concrete or construction not meet specified requirements.
Similarly, preventive surface treatments should not be needed within 20 years of construction unless to manage localised corrosion of non-structural steel.
Structures most likely to benefit from silane/siloxane treatment are those at risk from corrosion induced by contamination with chloride ions from seawater or seaspray, ie those in the NZS 3101 exposure classifications B2 (coastal frontage) and C (tidal/splash/spray). Bridges in exposure classifications A2 and B1 are unlikely to benefit, except where features related to design or construction have led to corrosion of non-structural steel, or where localised corrosion of structural steel suggests a more widespread problem.
The influence of surface treatments on the service lives of concrete bridges
Within the population of bridges in the B2 (coastal frontage) and C exposure classifications, groups of bridges at increased risk from corrosion because of particular design features (eg prestressed, or with low cover depths), or exposure to particular microclimates will benefit the most.
Individual bridges that may benefit from surface treatments are then identified by considering:
• the condition of concrete and reinforcement and how they would benefit from surface treatment
• the remaining service life required
• costs of access and other logistics
• whether it will be practical to maintain the treatment
• the effects on other surface treatments or remedial treatments that may subsequently be required.
Inspections to ascertain the potential benefits of treatment for a particular bridge should be carried out by specialists at least once every 20 years, in conjunction with Detailed Inspections.
The final decision to treat an individual bridge should not be based on economic evaluation alone, because an accurate evaluation is likely to cost a significant fraction of the treatment itself. In addition, NZ Transport Agency's current discount factor of 8% for maintenance works is unlikely to support preventive surface treatments on a life cycle benefit:cost basis. Instead, the decision-making process should involve a combination of economic evaluation and engineering judgement based on site investigation and testing to assess the actual condition of the structure and the risks of corrosion with and without surface treatment. If the NZ Transport Agency wishes to promote the use of preventive maintenance such as surface treatments, it could consider reducing the discount factor used for maintenance works.
Specifications for applying surface treatments to New Zealand bridges should be prepared by specialist consultants or based on suppliers' specifications, or APAS (2009) or other standard Australian specifications.
Once a preventive surface treatment has been applied, ongoing monitoring of its water resistance and of corrosion activity is required to ensure that the treatment is maintained at appropriate intervals. This monitoring should be carried out in conjunction with six-yearly Detailed Inspections. If the treatment is applied as a trial, such monitoring will indicate when untreated surfaces may need treatment or repair.
7 Recommendations
The following recommendations are proposed as a means of managing an identified risk to the performance of the New Zealand bridge stock by applying a preventive surface treatment to delay the onset of reinforcement corrosion and slow its subsequent rate before damage becomes significant. Thus, corrosion risk is addressed in a similar way to current seismic and scour risk-screening projects, whereby groups of bridges at most risk are identified, and then the needs of individual bridges within those groups are assessed in more detail to identify an appropriate means of addressing them.
7.1 Recommendations for NZ Transport Agency policy
These recommendations aim to improve corrosion risk management on concrete bridges by amending the NZ Transport Agency's existing policies and processes for bridge asset management. The proposed amendments would enable corrosion risk-screening to be carried out readily within the existing policies, and would encourage preventive maintenance, such as the application of surface treatments, to be undertaken more routinely. It is recommended that:
1
the NZ Transport Agency's Regional Asset Management Plans be amended to include
mandatory investigations of bridges in the following categories, which were identified in this research as being at high risk from reinforcement or prestressed steel corrosion:
Bridges of any age, in any exposure environment where localised corrosion (eg of individual
elements) indicates that corrosion is likely to become more widespread in future.
Bridges more than 20 years old that are exposed to seawater splash or seaspray, ie in
NZS 3101 exposure classifications B2 (coastal frontage) or C (tidal/splash/spray). Prestressed structures within 200m of open surf are a particularly high priority, especially those built before the mid-1970s.
Such investigations should be carried out by specialists as Special Inspections, to identify the corrosion risk and the need for treatment on individual bridges. They should coincide with Detailed Inspections and be carried out at least once every 20 years, the frequency being determined by the risk factors associated with each individual bridge.
2
the NZ Transport Agency's Bridge Inspection Policy (NZ TRANSPORT AGENCY:S6, 2009) be
amended to include Special Inspections for identifying the corrosion risk on individual bridges.
3
the NZ Transport Agency consider reducing the discount factor used for maintenance works.
By increasing potential long-term economic benefits, this would help promote preventive maintenance such as surface treatments.
The influence of surface treatments on the service lives of concrete bridges
7.2 Recommendations for asset owners/managers
These recommendations provide a basis for evaluating the potential benefits of surface treatment for a particular structure or group of structures, and are based on the conclusions presented in section 6.
1 When a surface treatment is applied as part of a repair system, it should be extended as a
preventive treatment to other elements on the bridge that do not currently need repair.
2 Surface treatments should be considered for extending the time to corrosion initiation and/or the
time to corrosion damage on reinforced or prestressed concrete elements. They should not be used to reduce corrosion rates once corrosion damage is evident, unless applied as part of a repair system.
3 Contracts for the construction of new bridges should allow for adequate site supervision to ensure
that the depth and quality of concrete cover comply with the project specification, which in turn must comply with the minimum requirements of current New Zealand standards.
4 For maximum cost-effectiveness, surface treatments should be applied when corrosion initiation is
imminent, but before corrosion damage is apparent. Treatment of reinforced concrete may be delayed until close to, or slightly after, corrosion initiation, provided that the risk associated with a small amount of corrosion is acceptable. Purposely delaying treatment of prestressed concrete until close to or after corrosion initiation is not recommended, however, because even a small amount of corrosion can significantly reduce structural performance.
5 Surface treatments should be considered for extending the service life of concrete bridges in the
following categories:
New bridges, to supplement repairs or other surface treatments where the quality of materials
or construction does not meet specified requirements.
Bridges of any age in any exposure environment where localised corrosion (eg of individual
elements) indicates that more-widespread corrosion is likely in future.
Bridges more than 20 years old exposed to seawater splash or seaspray, ie in NZS 3101
exposure classifications B2 (coastal frontage) or C (tidal/splash/spray). Prestressed structures within 200m of open surf are a particularly high priority.
6 Surface treatments should be considered for individual bridges within the above categories where a
Special Inspection to identify the corrosion risk finds that:
chloride ion profiles indicate that chloride concentrations will reach corrosion threshold levels
at the reinforcement within 15 years
corrosion risk is locally elevated on single elements, or parts of elements
chloride ion concentrations have reached threshold levels over much of the element or
structure, but the reinforcement is not sufficiently corroded to damage the concrete or significantly reduce the steel cross section.
7 Recommendations
7 The priority for treating individual bridges within the above categories should be evaluated by
direct and indirect costs of treatment
the current condition of the concrete and reinforcement
time to corrosion initiation (including measurement of chloride ion profiles and reinforcement
remaining service life requirements
whether maintaining the treatment at the required intervals will be practical
the risk and indirect costs associated with future reduced levels of service that may result from
corrosion of elements on which the treatment is not maintained
the effect of the treatment on other surface or remedial treatments that may subsequently be
risks and costs associated with not applying a surface treatment.
8 Evaluations based on experience, engineering judgement and simple predictions of service life,
with and without treatment, are recommended for most cases. Statistically based evaluations of service life and life cycle costs, with and without treatment, may be worth considering on very large structures, but are unlikely to be cost effective for most New Zealand bridges.
9 For bridges within the above categories, Special Inspections should be carried out at least once
every 20 years to identify the corrosion risk on individual bridges to support the evaluation. These investigations should be carried out by specialists in conjunction with Detailed Inspections, the frequency depending on the risk factors associated with the individual bridge.
10 Silane/siloxane surface treatments, rather than pore-blocking treatments, should be used to
reduce the risk of chloride-induced corrosion. Pore-blocking treatments may be used if the supplier can demonstrate that the product meets silane/siloxane performance requirements for breathability and for controlling ingress of chloride ions and moisture.
11 Silane/siloxane or pore-blocking treatments may be considered for reducing the rate of
carbonation-induced corrosion. If the cover concrete contains chloride ions, then the effect of the surface treatment on carbonation needs to be considered, not only in terms of its effect on carbonation-induced corrosion, but also on the distribution of chlorides that may be present in the cover concrete. Application of an anti-carbonation coating, such as an acrylic membrane, may be beneficial where the quality and/or depth of cover concrete provides insufficient protection from the ingress of moisture and air, or where carbonation may increase the risk of chloride-induced corrosion.
12 Silane/siloxane treatments should not be applied to new structures as part of the construction
process, except to supplement repairs or other surface treatments where the quality of materials or construction does not meet specified requirements.
The influence of surface treatments on the service lives of concrete bridges
13 Acceptance of silane/siloxane treatments should be based on APAS (2009) or other Australian
standard specifications. Alternative specifications may be used, provided the specified tests can be readily procured.
14 Acceptance of pore-blocking treatments should be based on the supplier demonstrating
compliance of material and application with international standard specifications.
15 Silane/siloxane treatments must be reapplied regularly to maintain their effectiveness.
16 For asset management and economic evaluation purposes, an interval of 10–20 years between
applications should be assumed, depending on exposure conditions.
17 When a structure has been treated, future maintenance plans should provide for monitoring the
performance of the treatment and the condition of treated concrete at every Detailed Inspection, to determine the need for repeat application.
18 Bridge asset managers should report their experiences with preventive surface treatments, so that
others in the bridge design and management communities can benefit from it.
References
Alberta Transportation (2007)
Specification for bridge construction: Section 4 – Cast-in-place concrete.
Alberta Transportation (2008) Best practice guidelines for selecting concrete bridge deck sealers.
Accessed 1 June 2010.
www.transportation.alberta.ca/Content/docType253/Production/BrSealerGdln.pdf
Alberta Transportation (2009) Specification for concrete sealers.
Technical Standards Branch, B388-
January 2009. 8pp.
Attanayake, U, X Liang, S Ng and H Aktan (2006) Penetrating sealants for concrete bridge decks –
selection procedure.
Journal of Bridge Engineering 11, no.5: 533–540.
Australian Paint Approval Scheme (APAS) (2009) Silane based water repellents for concrete and
masonry.
APAS Specification AP-TS0168, CSIRO Materials Science and Engineering Div 1. 8pp.
Bamforth, PB (2004) Enhancing reinforced concrete durability: guidance on selecting measures for
minimising the risk of corrosion of reinforcement in concrete.
The Concrete Society (UK) Technical Report 61, Part 1.
Bassi, R and SK Roy (2002)
Handbook of coatings for concrete. Scotland: Whittles Publishing.
British Standards Institute (2004) Products and systems for the protection and repair of concrete
structures – definitions, requirements, quality control and evaluation of conformity: Part 2 – surface protection systems.
BS EN 1504-2:2004.
Bruce, SM, PS McCarten, SA Freitag and LM Hasson (2008) Deterioration of prestressed concrete bridge
beams.
Land Transport New Zealand research report 337. 76pp.
Calder AJJ (2002) Effectiveness of silane treatment on preventing the ingress of chloride ions into
concrete bridge piers – Report of chloride sampling on Lye Lane Bridge (April 2002). TRL Specimen Monitoring Project. 11pp.
Calder, AJJ (2006) The effectiveness of silane in reducing rates of corrosion in reinforced concrete.
Interim report of monitoring laboratory specimens (January 2006). TRL Specimen Monitoring Project. 12pp.
Calder, AJJ, N Anderson and M McKenzie (2006) Survey of impregnated structures.
TRL Published
Project Report PPR136. 33pp.
Calder, AJJ and M McKenzie (2009) Performance of impregnants.
TRL Published Project Report PPR362.
Chirgwin, G, P Manamperi and M Moore (2009) A global study of chloride induced corrosion within the
RTA's reinforced concrete bridge stock.
Austroads Bridge Conference, 26–29 May 2009, Auckland.
Construction Industry Research and Information Association (CIRIA) (1987) Protection of reinforced
concrete by surface treatments.
CIRIA Technical Note 130. 72pp.
The influence of surface treatments on the service lives of concrete bridges
Dai, J-G, Y Akira, FH Wittman, H Yokota and P Zhang (2010) Water repellent surface impregnation for
extension of service life of reinforced concrete structures in marine environments: the role of cracks.
Cement and Concrete Composites 32, no.2: 101–109.
Darby, JJ, GP Hammersley and MJ Dill (1996) The effectiveness of silane for extending the life of
chloride contaminated reinforced concrete. In
3rd International Conference on Bridge Management, University of Surrey, Guildford, UK, 14–17 April 1996: 838–848.
Department of Infrastructure, Energy and Resources Tasmania (DIER) (2006) Penetrating sealers and
coatings for concrete.
Bridgeworks Specification B23, October 2006. 4pp.
Department of Infrastructure, Energy and Resources Tasmania (DIER) (2006) Concrete repairs.
Bridge
Maintenance Specification B15, October 2006. 5pp.
Department for Transport (England) (2005) Management of highway structures: a code of practice.
Norwich: The Stationery Office.
Freitag, SA, WE Hickman SM and SM Bruce (2003) Cost effective remedial techniques for reinforcement
corrosion in concrete bridges.
Transfund New Zealand research report 251. 78pp.
Highways Agency (UK) (1986) Materials for the repair of concrete highway structures.
Design manual
for roads and bridges 3, section 3. BD27/86.
Highways Agency (UK) (2003) The impregnation of reinforced and prestressed concrete highways
structures using hydrophobic pore-lining impregnants. In
Design manual for roads and bridges, vol. 2, section 4, part 2, BD 43/03.
Highways Agency (UK) (2004a) Specification for highway works, vol 1, clause 1709. In
Manual of
contract documents for highway works (May 2004 amendment): 6–7.
Highways Agency (UK) (2004b) Coatings for concrete highway structures and ancillary structures. In
Design manual for roads and bridges 2, section 4, part 3, BA 85/04.
Highways Agency (UK) (2009) Value management of the structures renewal programme.
Highways
Agency guidance document version 3.3 (and preceding versions). London: Highways Agency.
Ho, DS and D Ritchie (1992) Surface coatings and their influence on the quality of the concrete
substrate. In
Proceedings Rehabilitation of Concrete Structures. DS Ho and F Collins (Eds): 403–407. RILEM/CSIRO/ACRA, Melbourne, 1992.
Ibrahim, M, AS Al-Gahtani, M Maslehuddin and FH Dakhil (1999) Use of surface treatments to improve
concrete durability.
Journal of Materials in Civil Engineering 11, no.1: 36–40.
Jandu, AS (2008) Inspection and maintenance of highway structures in England. Institution of Civil
Engineers,
Bridge Engineering 161, issue BE3: 111–114.
McCarter, WJ, BT Linfoot, TM Chrisp and G Starrs (2008) Performance of concrete in XS1, XS2, and XS3
environments.
Magazine of Concrete Research 60, no.4: 261–270.
McGettigan, E (1992) Silicon-based weatherproofing materials.
ACI Concrete International 14, no.6: 52–
Nanukuttan, S, L Basheer, WJ McCarter, DJ Robinson and PAM Basheer (2008) Full-scale marine
exposure tests in treated and untreated concretes – initial 70 year results.
ACI Materials Journal, Jan–Feb 2008: 81–87.
NZ Transport Agency (2009)
Bridges and other structures inspection policy (S/6). Wellington: NZ
Transport Agency.
NZ Transport Agency (2010)
Economic evaluation manual – volume 1 (EEM 1). Wellington: NZ Transport
Ng, A (2006) Techniques to combat corrosion of steel in concrete.
VicRoads Design, Research and
Development Report 948. 148pp.
Pearson, S and JR Cuninghame (1998) Water management for durable bridges.
Transport Research
Laboratory, Application Guide 33. 165pp.
Peek, AM and MG Ali (2001) Corrosion performance evaluation of Aquron 7000 system on an existing
marine structure. Paper 012 in
Proceedings, Corrosion and Protection 2000, Australasian Corrosion Association, Auckland.
Perenchio, WF (1988) Durability of concrete treated with silanes.
Concrete International 10, no.11: 34–
Raupach, M and L Wolff (2005) Long term durability of hydrophobic treatment on concrete.
Surface
Coatings International: Part B – Coatings Transactions 88, B2:127–133.
Salome, F and H Morris (1997) Specifications for concrete impregnation. In
Austroads Bridge
Conference, 1997: 43–55.
Sandeford, P, G Bendell and A Mansoor (2009) Corrosion management strategy for reinforced concrete
wharf infrastructure located at the mouth of the Brisbane River.
Corrosion and Materials 34, no.6: 32–37.
Smith, E and P Simpson-Bint (2009) Show me the money!
Austroads Bridge Conference, 26–29 May
Sohanghpurwala, AA (2006) Manual on service life of corrosion-damaged reinforced concrete bridge
superstructure elements.
Transportation Research Record 558: 59pp.
Song, G and A Shayan (1999) Corrosion prevention of reinforced concrete structures.
ARRB Research
Report 332. 112pp.
South Carolina Department of Transportation (SCDoT) (2007) Qualified policy for silane bridge deck
sealers.
Qualified Product Policy 27.
Standards Australia (2005) Guidelines for the design of maritime structures.
AS 4997-2005.
Standards New Zealand (1997) Concrete construction.
NZS 3109:1997. Wellington: Standards New
Standards New Zealand (2003) Specification for concrete production.
NZS 3104:2003. Wellington:
Standards New Zealand.
The influence of surface treatments on the service lives of concrete bridges
Standards New Zealand (2006) Concrete structures standard: Part 1 – The design of concrete
structures.
NZS 3101:Part 1:2006. Wellington: Standards New Zealand.
The Concrete Society (1997) Guide to surface treatments for protection and enhancement of concrete.
The Concrete Society (UK) Technical Report 50. 80pp.
Titarelli, F and G Moriconi (2008) The effect of silane-based hydrophobic admixture on corrosion of
reinforcing steel in concrete.
Cement and Concrete Research 38, no.11: 1354–1357.
Vassie, PR and A Calder (1999) Reducing chloride ingress to concrete bridges by impregnants. In
Proceedings International Seminar –
Controlling concrete degradation. RK Dhir (Ed). Dundee:133–147.
VicRoads (2002)
VicRoads bridge maintenance repair and strengthening guidelines (rev 2003). Victoria:
Roads Corporation. 115pp.
VicRoads (2009) Structural concrete.
VicRoads Contract Documents: Series 600 – Bridgeworks, Section
610. Victoria: Roads Corporation.
VicRoads (2009) Coating of concrete.
VicRoads Contract Documents: Series 600 – Bridgeworks, Section
Weyers, R, B Prowell, M Sprinkel and M Vorster (1993) Concrete bridge protection, repair and
rehabilitation relative to reinforcement corrosion: a methods application manual.
Strategic Highway Research Program report SHRP-S-360. 268pp.
Weyers, RE, MG Fitch, EP Larsen and IL Al-Qadi (1994) Service life estimates.
Strategic Highway
Research Program report SHRP-S-668. 357pp.
Weyers, RE, J Zemajtis and RO Drumm (1995) Service lives of concrete sealers.
TRRB 1490: 54–59.
Zemajtis, J and RE Weyers (1996) Concrete service life extension using sealers in chloride-laden
environments.
TRRB 1561: 1–5.
Appendices
The influence of surface treatments on the service lives of concrete bridges
Appendix A Examples of specification limits
Typical or specified penetration depths
Reference
Test method
Product type
Spec. limit
Solvent-free silane
VicRoads Spec 686
Silane-siloxane,
<10mm (class I)
≥10mm (class II)
defined by the penetration depth
Also see table A5
Notes to table A1:
(a) If required, a test area at least 1m2 is to be treated prior to commencement of the work, and the penetration
depth measured. This provides a standard and control for future work.
(b) Minimum water uptake before and after abrasion specified as an indicator of satisfactory performance at depth
from treated surface.
Typical or specified water absorption characteristics
Reference
Test method
Product type
Spec. limita
Solvent-free silane
VicRoads Spec 686
BS 1881 Part 5c All
≤0.01ml/m2.s -
EN 13580d Hydrophobic
1062-3e Impregnation <0.1kg/m2.h0. e -
Silane (type 1a)
Transportation B388 (2009)
Notes to table A2:
(a) % of untreated control sample unless an absolute value or a % reduction is quoted – see notes to individual test
methods for a description of the property measured.
(b) Reduction in water uptake.
(c) ISAT test after 10 minutes.
(d) Rate of weight gain.
(e) Capillary absorption and permeability.
(f) If required, a test area at least 1m2 is to be treated prior to commencement of the work. The reduction in
absorption of a treated surface compared with an untreated surface may then be used as a standard and control for future work.
The influence of surface treatments on the service lives of concrete bridges
Typical or specified water vapour transmission characteristics
Reference
Test method
Product type
Spec. limita
EN 13579b Hydrophobic >30% (class I)
>10% (class II)
defined by the penetration depth
Impregnation <5m
5–50m (class II)
>50m (class III)
penetration depth
Notes to table A3:
(a) % of untreated control sample – see notes to individual test methods for description of the property measured.
(b) Rate of weight loss.
(c) Permeability to water vapour.
Typical or specified chloride ion resistance characteristics
Reference
Test method
Product type
Spec. limita
Solvent-free silane
>80% @ 0–5mm
>90% @ 10–25mm
>75% @ 0–5mm
>80% @ 10–25mm
VicRoads Spec 686 See note (c)
Moisture and chloride
<5x10-9cm2/s -
Notes to table A4:
(a) % of untreated control sample.
(b) Reduction in chloride uptake.
(c) Chloride diffusion for coatings used for moisture and chloride resistance (no method specified).
(d) When the capillary water absorption is <0.01kg/m2.h0.5.
The influence of surface treatments on the service lives of concrete bridges
Durability indicators (notes to table are on the following page)
Reference
Test method and
Product type
Spec. limita
property
alkaline surface; guaranteed recoat period ≥10yrs
Observed loss of
water repellancyh
NCHRP 244c Silane
solution ≤20% - -
BD 43/03 App. Ab;
proven evidencei
EN 13580b Hydrophobic <10% - -
No bubbles, cracks
EN 13687-1, -2, -3
or delamination;
Within 3% of the
Alkali resistance
Notes to table A5:
(a) % of untreated control sample, unless otherwise stated – see notes to individual test methods for description of
the property measured.
(b) Reduction in water uptake after exposure to alkaline solution, compared to water uptake of treated samples not
exposed to alkaline solution.
(c) Reduction in water uptake and chloride uptake after accelerated weathering.
(d) Reduction in pull-off strengths after exposure to cycles of immersion in salt solution (if appropriate) and/or
thermal cycling. Limits quoted are averages for horizontal, vertical (no mechanical load) and vertical (with mechanical load) applications.
(e) Reduction in absorption measured after abrasion.
(f) After exposure to alkali, waterproofing performance after abrasion must be within 3% of performance after
abrasion only (method BT001).
(g) Must be resistant to cleaning with water at 50–60°C, detergent and scrubbing without softening, loss of
adhesion, or change in colour or gloss.
(h) Indicates that recoating could be required in approximately 15 years as the coating begins to fail, allowing
droplet and chloride ingress.
(i) Documented evidence required to show that impregnants maintain a water-repellent vapour-permeable surface
for at least 15 years after application.
The influence of surface treatments on the service lives of concrete bridges
Appendix B Deterioration of reinforced concrete
Many conceptual models have been used to describe reinforcement corrosion in terms of how the damage affects the overall serviceability of reinforced concrete. Some of these are presented in figures B1–B3.
These models identify two phases of deterioration:
1
Initiation phase: During this phase, chloride ion contamination and/or depth of carbonation
gradually increase until chloride ion contamination at the reinforcement reaches a threshold concentration, or carbonation reaches the reinforcement. The duration of the corrosion initiation phase is the ‘time to corrosion initiation'. The end of this phase is shown in figure B3 as limit state 1. Corrosion may or may not start at the end of this phase, depending on whether sufficient water and oxygen are available. Many corrosion prediction models estimate the time to corrosion initiation.
2
Propagation phase: During this phase, carbonation depth and chloride ion concentrations in the
concrete continue to increase, the reinforcement starts to corrode, and the level of damage progressively increases. The duration of this phase depends on the rate of corrosion and the definition of ‘unacceptable damage' that marks the end of service life. The corrosion rate is determined by the availability of moisture and oxygen. The level of damage regarded as unacceptable may be any one of the following limit states:
a
Time at which corrosion damage becomes likely – the time when corrosion rates and the
likelihood of damage become significant (but cracks may not yet have developed) may be difficult to detect by normal routine inspection methods, or may be considered too minor to warrant further investigation
b
Time to first crack – the time when corrosion products have generated sufficient pressure to
crack the cover concrete, which is usually the first visible sign of rebar corrosion
Time to first spall – the time when corrosion products have generated sufficient pressure to
spall the cover concrete – on some structures, spalling concrete may be structurally acceptable
but hazardous to traffic or pedestrians or the environment
d
Significant loss of steel cross section – the time when reinforcement performance is reduced
e
Loss of structural integrity – the time when the performance of the affected element is
The definition of ‘bridge design life' used in the NZ Transport Agency's Bridge Manual is ‘the life beyond which the bridge will be expected to become functionally obsolete, or to have become uneconomic to maintain in a condition adequate for it to perform its functional requirements'. Some maintenance and repair is allowed during this period. Depending on the risks associated with the individual structure, state 2b, 2c or 2d may represent the NZ Transport Agency definition of ‘end of service life', whereby a bridge is no longer economic to maintain.
The cost of repair is proportional to the level of damage, so the models presented in figure B also illustrate how repair costs increase with time and level of damage.
Preventive maintenance may be carried out until state 2a. Repair is necessary after state 2b. Preventive maintenance may be effective between states 2a and 2b if no damage has occurred, but will not be effective if damage has occurred but not been detected.
Patch repair of cover concrete may be sufficient until the end of state 2d, after which structural repair with replacement of steel is necessary.
Examples of deterioration models and limit states
Figure B.1
Traditional model (from Bamforth 2004)
The influence of surface treatments on the service lives of concrete bridges
Figure B.2
Progressive contamination model (from Bamforth 2004)
Figure B3
Suggested limit states (indicated by horizontal lines) in progressive contamination model
(2a) Corrosion damage becomes likely
(2b) First crack detected
(2c) First spall
(2d) Loss of steel cross section
(2e) Loss of structural integrity
The time intervals between each state will vary between structures.
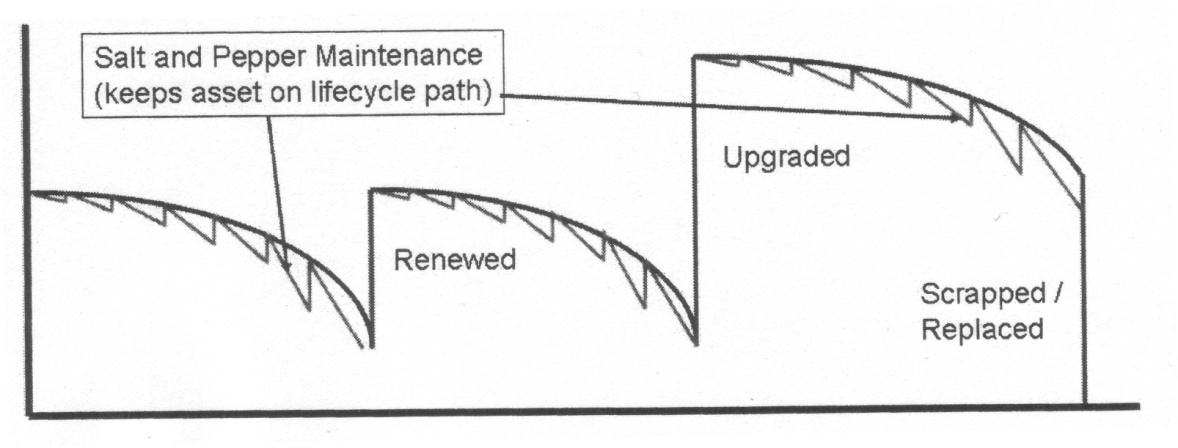
The influence of surface treatments on the service lives of concrete bridges
Appendix C Impact of cyclical maintenance on life cycle
Figure C.1 below was presented in Smith and Simpson-Bint (2009) as a model to describe how regular routine maintenance maintains a bridge asset on its expected life cycle, including phases of renewal and upgrading. Thus they describe the short zigzag lines as representing how regular maintenance to satisfy community expectations (or other levels of service) maintains the asset on its normal life cycle path and does not restore the consumed future economic benefit. Lack of regular maintenance increases the expenditure needed (the size of the zigzag) when maintenance is carried out to restore the asset to its life cycle path. Lack of routine maintenance causes the path to deviate downwards from the life cycle curve to a premature need for replacement.
Figure C.1
Prabhu-Edgerton consumption model (from Smith and Simpson-Bint 2009)
Source: http://nzta.govt.nz/resources/research/reports/403/docs/403.pdf
Justicia de GéneroViolencia sexual en conflictos armados: el derecho de las mujeres a la justicia Luego de la entrega del Informe Final de la Comisión de la Verdad y Reconciliación (CVR) en el año 2003, DEMUS decide contribuir a Estudio para la Defensa que sus recomendaciones se concreten; en particular las que permi- de los Derechos de la Mujer
INTELLECTUAL PROPERTY Which intellectual property PUBLISHING MANAGER strategy firm delivers more Charles Orton-Jones DESIGN, ILLUSTRATION, INFOGRAPHICS of the World's Top 300 IP Strategists than any other? Freelance writer, based in Madrid, he specialises in the international economy, emerging markets,